Системы управления холодильным и компрессорным оборудованием
Холодильная установка - комплекс холодильных машин и дополнительного оборудования, применяемый для искусственного охлаждения.
Дополнительное оборудование холодильной установки включает оборудование для охлаждения и подачи охлаждающей воды, приготовления и подачи хладоносителя и теплоносителя. Технологическое оборудование потребителей в состав холодильной установки, как правило, не входит.
В комплексе с холодильной машиной находятся и системы управления. Управление различными узлами и аппаратами, участвующими в процессе переноса тепла рабочим телом холодильной машины. Системы управления могут быть самыми различными: от простых двухпозиционных до сложнейших систем управления, построенных на математическом моделировании процесса с решением сложных интегральных и дифференциальных задач. Посредством решения математических задач формируется управляющее воздействие системы как ответная реакция на изменения рабочего процесса с целью поддержания заданных условий и параметров процесса.
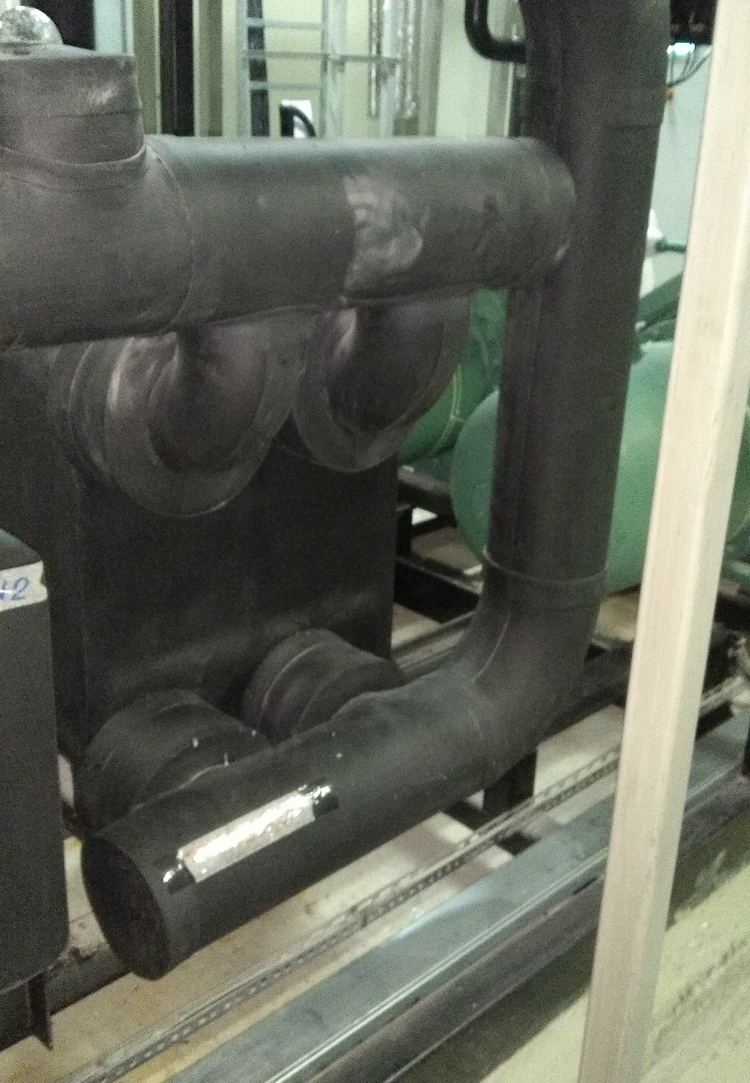
Процесс суточного колебания температуры хладоносителя при охлаждении ледового поля
С целью повышения эффективности работы установки, а также снижения издержек эксплуатации, АПК должен периодически обновляться. Потеря качественных свойств основных компонентов холодильного или гидравлического контура, должна компенсироваться совершенствованием АПК, учитывающим эти изменения.
Также в структуру развиваемого АПК, нередко интегрируют новые защитные и следящие системы, которые обеспечивают отслеживание работы компонентов установки, находящихся в предельном рабочем состоянии. Практически все аппаратные комплексы не развивающиеся в процессе эксплуатации оборудования, всегда приводятк одним и тем же последствиям. Особенно явное, на изображении.
В процессе эксплуатации холодильной установки, наблюдается устаревание существующего аппаратно-программного комплекса (АПК), что объясняется потерей работоспособности основных элементов АПК в процессе длительной работы (физический износ) и невозможностью выполнения командных и следящих функций.
Среди негативных последствий влияния данных факторов можно выделить:
- Рост энергопотребления оборудования;
- Снижение эффективности работы оборудования;
- Нестабильность температурного режима;
- Снижение срока службы оборудования;
- Повышение издержек на энергоресурсы и ремонт установок.

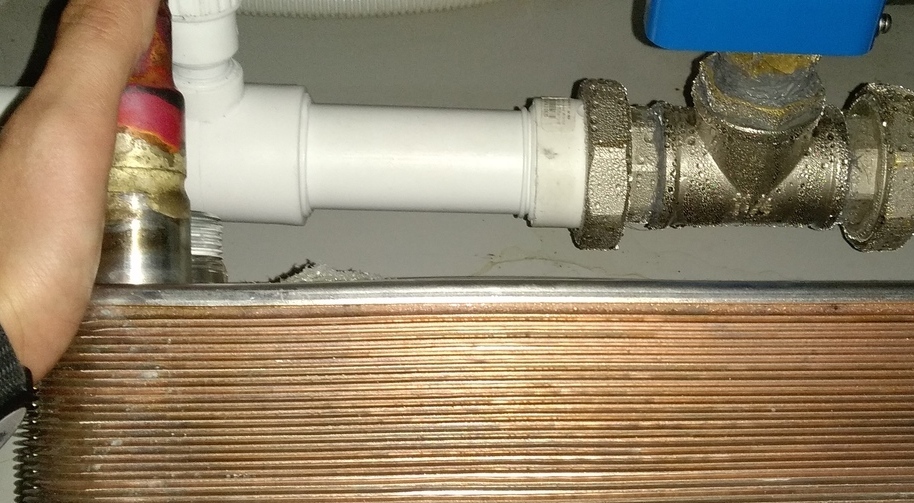
В части основных элементов парокомпрессорной холодильной машин входят: компрессор, конденсатор, испаритель и дроссель. Стоит разбить все системы управления холодильным оборудованием на 4 основные группы, каждая из которых относится к своему элементу. Однако, реальные холодильные машины, более сложные чем идеальная. Множество различных самостоятельных систем, которые являются вспомогательными и им посвящена отельная пятая группа.
Группа 1. Компрессор. Компрессорный агрегат
Компрессорный агрегат в составе холодильной машины является её "сердцем". Система управления компрессорным агрегатом сочетает в себе наиболее эффективные и продвинутые аппаратные и программные решения, созданные для максимально эффективного использования электрической энергии и повышения надёжности холодильной машины.
Для управления компрессорным агрегатом холодильной машины используются т.н. контроллеры производительности. Как правило, существет одна главная обратная связь, по которой происходит управление работой компрессоров.
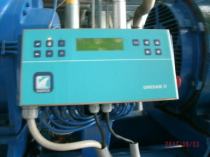
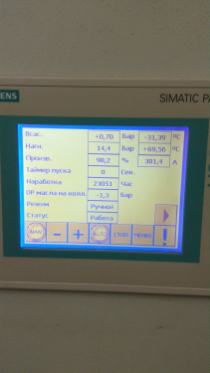
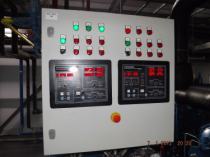
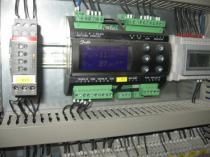
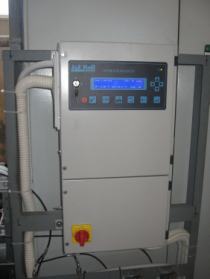
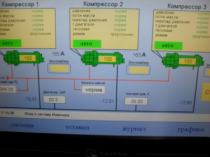
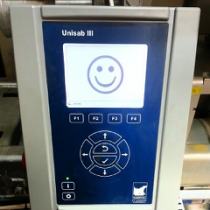
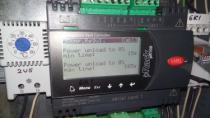
Холодильный агрегат Copeland ZB 56
Холодильный агрегат Dorin H2500
Холодильный агрегат J&E Hall HSM 4223
Холодильный агрегат Bitzer 6H
Холодильный агрегат Bitzer CSH
Производители контролеров предлагают широкий модельный ряд устройств для управления компрессорами как компактных холодильных машин, так и больших холодильных установок. Современные интеллектуальные контроллеры позволяют добиваться максимальной энергоэфективности за счет использования дополнительных устройств, подключаемых к контроллеру, таких как частотные преобразователи. Использование таких устройств позволяет плавно регулировать давление всасывания в зависимости от тепловой нагрузки и температуры окружающей среды. Кроме регулирования производительности системы, контроллер постоянно отслеживает состояние цепей защиты всех элементов компрессорного агрегата, что в совокупности с использованием систем самодиагностики, используемых в современных контроллерах повышает надежность работы системы.
Очень часто, в процессе осмотра оборудования установливается, что управление компрессором (объёмной подачей) происходит по результату работы всей холодильной установки. Иными словами можно сказать, что в логике управления заложена жёсткая связь, при которой результат работы компрессора, практически всегда тождественен результату работы всей установки, однако на практике это не совсем так. АСУ компрессора, получая информацию от датчика контроля процесса (давление пара охлаждаемой среды или температура хладоносителя), приходит к выводу о необходимости повышения производительности компрессора, оценивая ситуацию с ростом давления в технологии как повышение нагрузки. Такая формула практически всегда, расценивает повышение температуры технологи, как требование к набору мощности, если она не максимальная. Однако, нужно обратить внимание, что рост температуры технологии, даже без роста нагрузки фактически подводимой от неё, может быть связан в той же мере с потерей эффективности работы самой холодильной машины. В этой непростой ситуации АСУ компрессора, начинает неоправданно увеличивать мощность установки, пытаясь компенсировать, падение эффективности, зачастую ей же самой и вызванное. Это приводит к огромному перерасходу электроэнергии, а так же продолжительной работе оборудования за допустимыми пределами эксплуатации и резкому снижению его ресурса.
Также очень важно помнить, что нагрузка на компрессор нагрузка на всю холодильную установку становятся тождественными величинами, только в практически стационарном режиме. Режимы запуска и изменения производительности, приводят к резкому изменению нагрузки установки, на которую АСУ компрессорного агрегата реагирует с определнной задержкой. Именно в период этих запаздываний в реакции, происходят процессы, которые становятся источниками неутихающих колебаний контрольных значений. Иными словами, компрессорный агрегат работает в постоянном переходном процессе, не имея возможности стабилизировать режим. Постоянный переходный режим приводит к такой же нестабильности во всех частях холодильной установки.
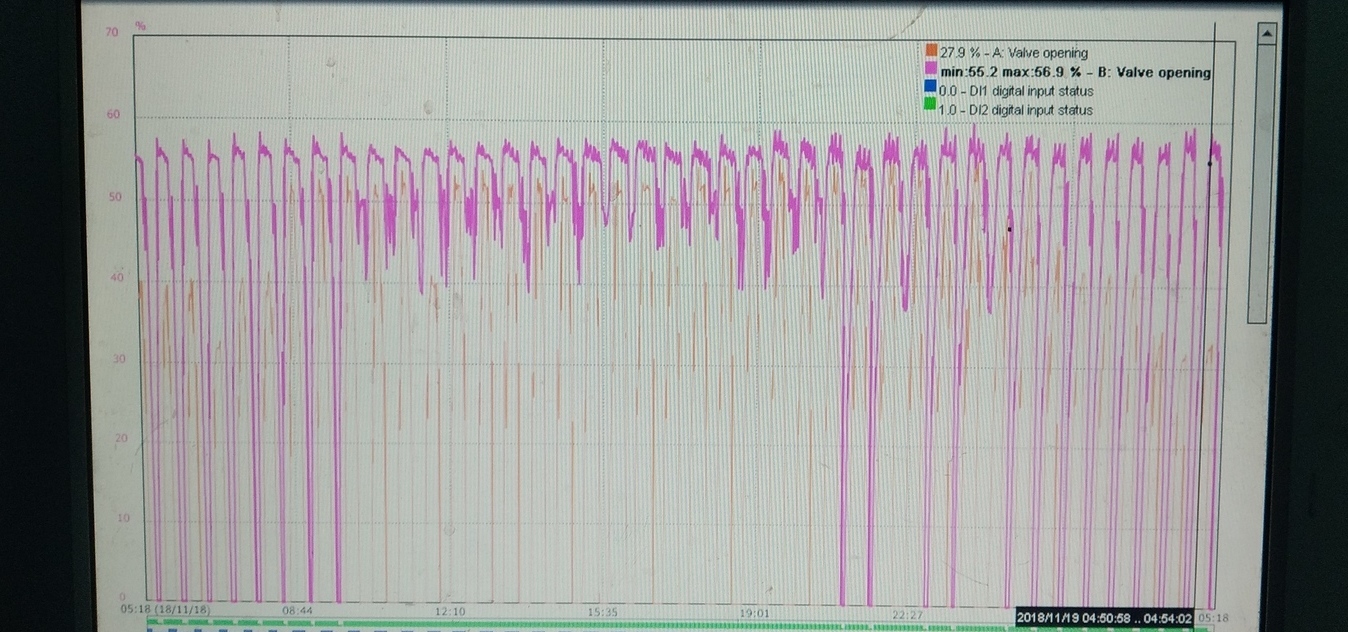
В настройке системы автоматического управления компрессорами, достаточно много нюансов, которые необходимо учитывать при эксплуатации оборудования. Так известно, что при золотниковом регулировании винтового компрессора, происходит падение его эффективности. Таким образом, при некорректной настройке АСУ, возможно получить такие режимы, при которых компрессоры, достаточно долго работают в режимах с низкой или очень низкой эффективностью.
Это же касается, вопросов контроля доведения сигнала АСУ до элементов компрессора, обеспечивающих изменение производительности.
Также стоит уделить внимание, тому факту что всё чаще "нерабочая" ступень 25% винтового компрессора, всё чаще становится полноценной ступенью регулирования.

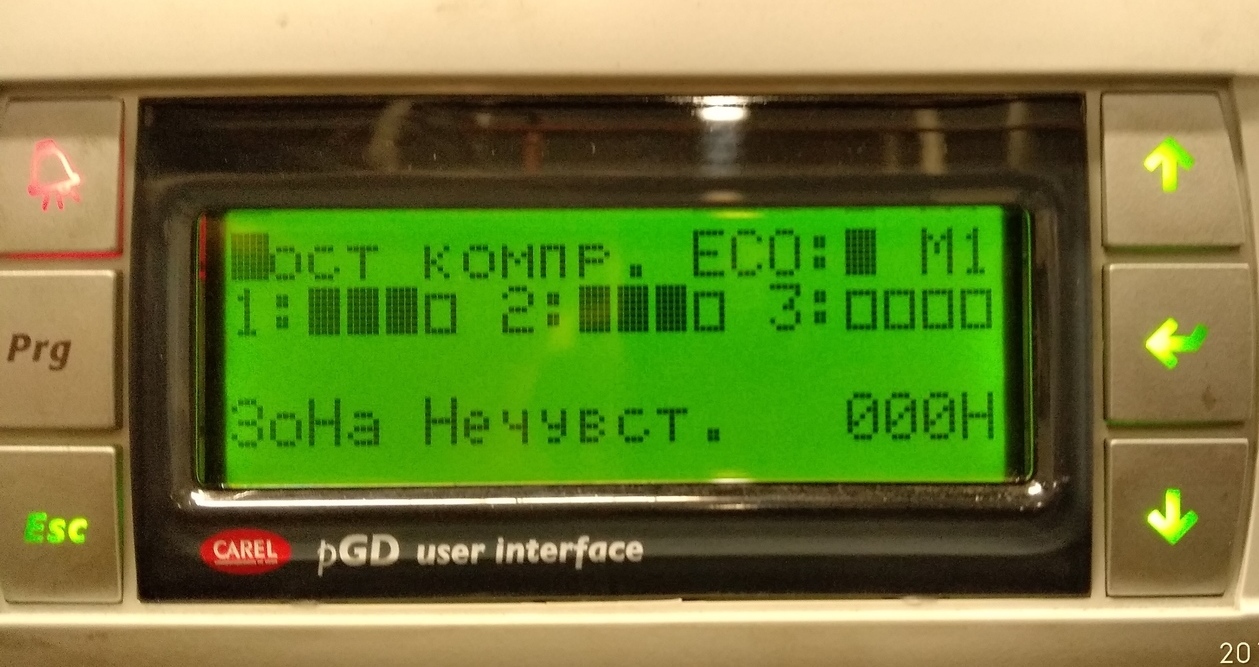
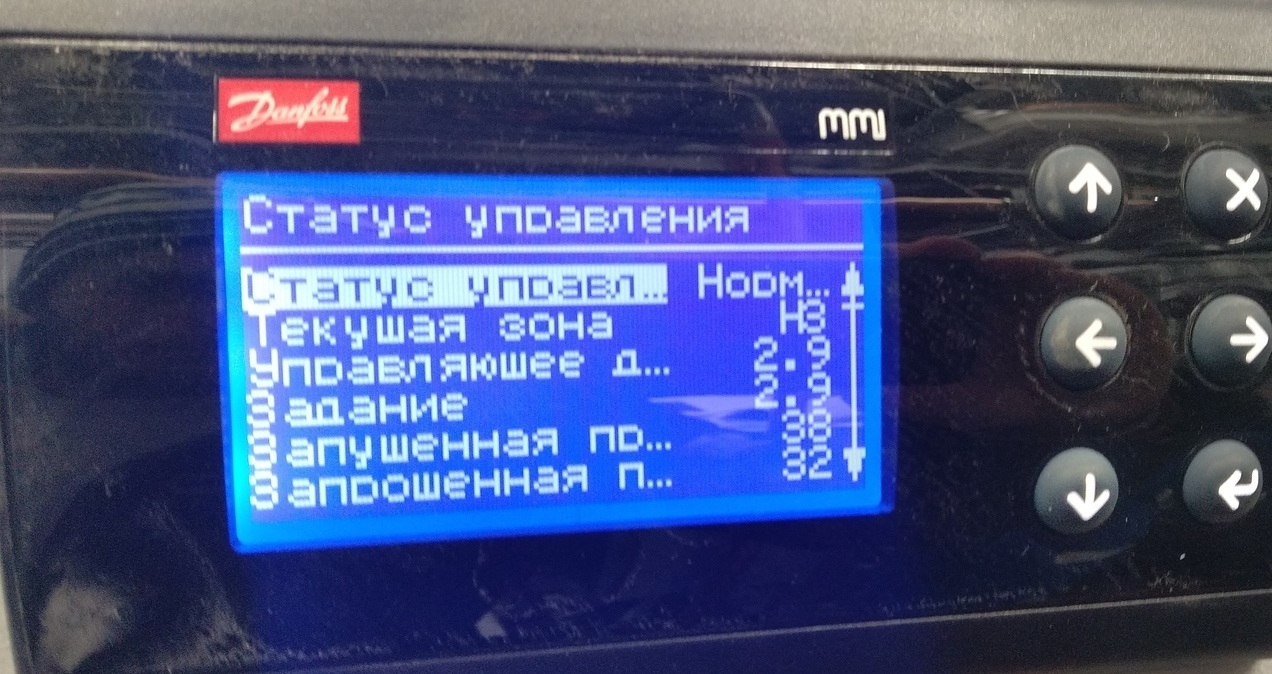
Одним из распостранённых способов регулирования компрессоров практически всех типов, является частотный привод. Использование частотного привода позволяет достаточно эффективно управлять производительностью компрессора. На практике используются частотные привода без входных и выходных фильтров. Это приводит к сильному искажению питающего напряжения, а так же к генерации в сеть большого количества помех. Это обусловлено принципом действия частотных преобразователей.
Работа агрегата без частотного привода основного компрессора, замер сигналов на общей ошиновке для всех потребителей.
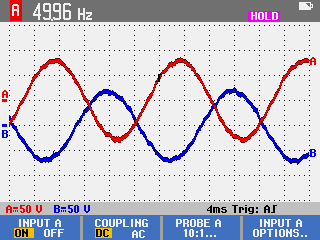
Работа агрегата с частотным приводом основного компрессора, замер сигналов на общей ошиновке для всех потребителей.
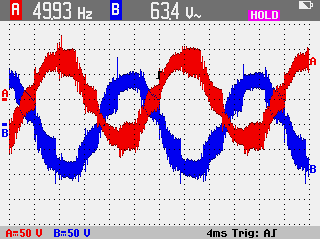
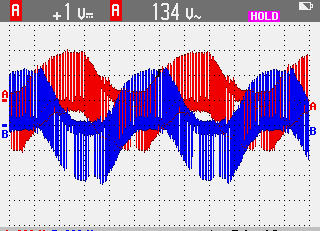
Общий вид сигнала поступающего на двигатель, по двум из линий и его спектр, с большим количеством отклонений. Частота ШИМ 4 кГц.
В обоих случая частотный привод не оснащён фильтром на входе (дроссель) и фильтром на выходе со стороны компрессора (синус-dU/dt)
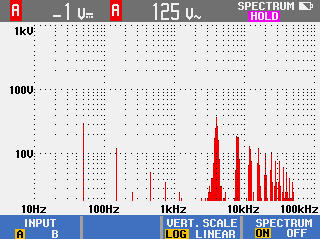

Очевидно, что сигнал такой формы, допускающий широкий разброс частот, а также импульсы высокого напряжения, должен привести к определённому результату - разрушению изоляции провода и отказу двигателя.
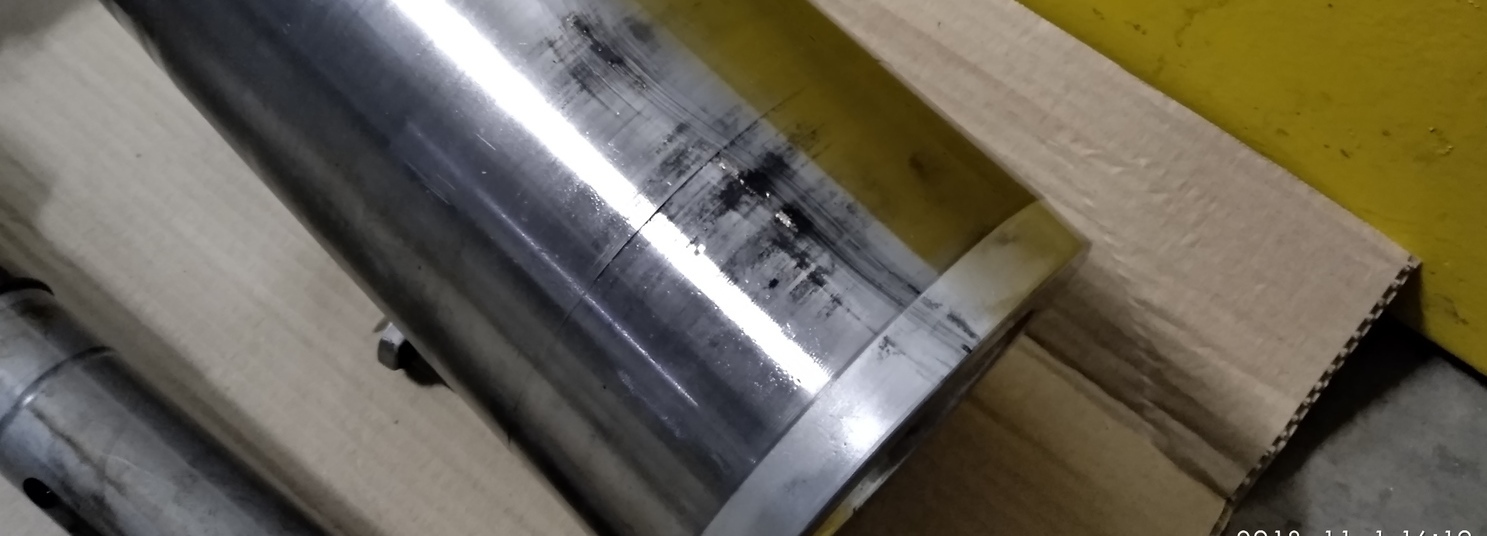
Частотные преобразователи, обеспечивающие регулирование производительности компрессора и вентиляторов конденсатора. Частотный преобразователь для вентиляторов конденсатора обеспечен фильтров выходного сигнала. Такой фильтр значительно повышает качество выходного сигнала преобразователя, что продлевает ресурс двигателей.
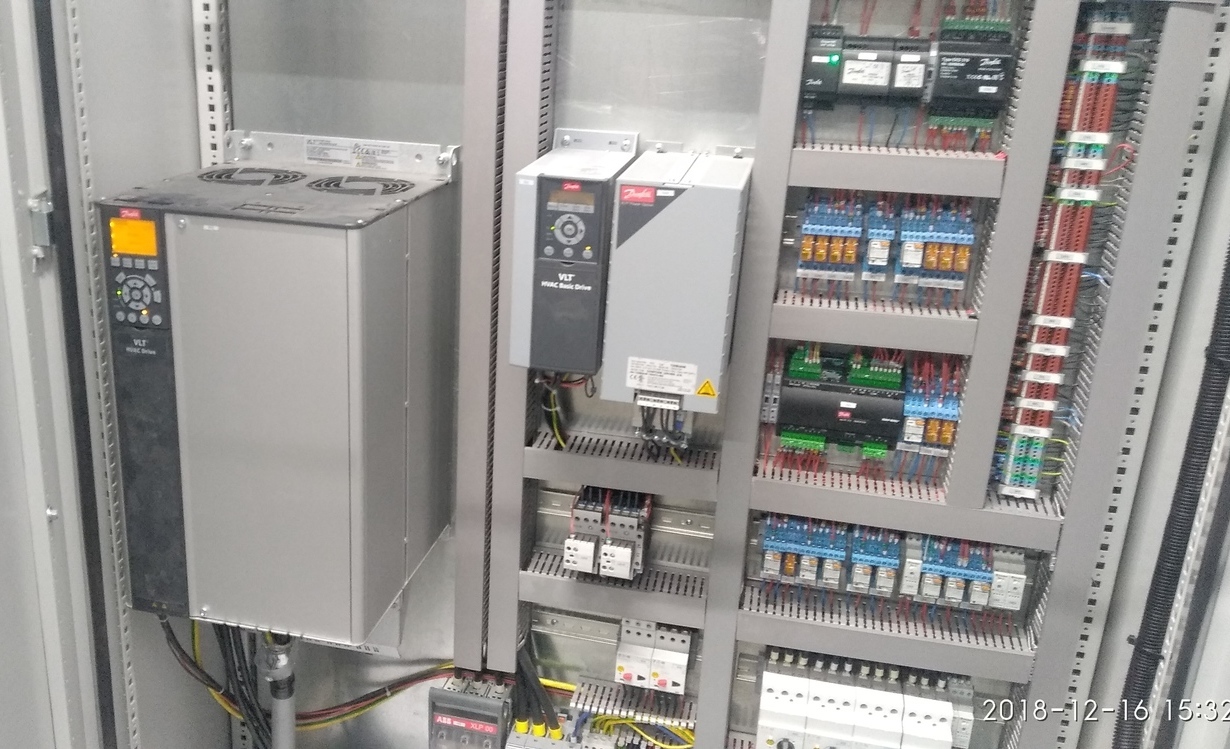
Группа 2. Конденсатор
Высокая эффективность работы конденсатора является непременным условием экономичной работы холодильной машины. Управление частотой вращения вентиляторов конденсатора, задвижкой на подчаче теплоносителя или частотой насоса, осуществляется контролером конденсатора при помощи частотного преобразователя или путем плавного управления клапаном. Контроль температуры конденсации относительно температуры охлаждающей среды даёт ощутимый прирост энергоэффективности, давая возможность снижать рабочий уровень давления до минимально возможного.
Группа 3. ТРВ. Электронные расширительные вентили
Питание испарителя холодильной машины, это залог высокой эффективности работы машины, а так же повышения её надёжности и ресурса. Регулярные выбросы жидкого холодильного агента из затопленного испарителя, практически всегда наносят серьёзный ущерб рабочим органам поршневого компрессора, даже если незначительные повреждения в момент попадания жидкости не влекут аварийной остановки, то важно помнить, что в дальнейшем развитие этих повреждений приводят к серьёзным авариям. Особенно если их катализатором служит термическая усталость материалов, вызванная циклами сильного нагрева и охлаждения.
Механическое ТРВ Alco Controls
Электронное ТРВ Danfoss ETS 12.5
Механический ТРВ TE 55 Danfoss
Электронный расширительный вентиль Carel ExV
Электронный расширительный вентиль Carel ExV
Механический ТРВ Alco Controls
Механический ТРВ Danfoss TE
Электронное ТРВ Sporlan
Группа 4. Испаритель
Трубная решётка воздухоохладителя
Разборный пластинчатый испаритель
Разборный пластинчатый испаритель
Управление испарителем осуществляется контроллером испарителя с помощью соленоидного клапана и дросселирующего устройства. Так же контроллер управляет процессами обеспечивающими надёжную и качественную работу испарителя, например, оттайки, работой вентиляторов испарителя и других агрегатов в составе которых используется испаритель. Контроллеры испарителя подключённые в систему мониторинга позволяют максимально эффективно использовать мощность компрессорного агрегата и повысить надёжность всей холодильной машины.
Переполнение жидким холодильным агентом испарителя и выпуск его на всасывание в компрессор, является процессом, приводящим к повреждениям компрессора и, как правило, не сопровождаются потерей эффективности со стороны технологии, а даже наоборот. Это связано с достаточным, или даже избыточным наполнением испарителя жидкостью, что вовлекает дополнительную площадь для осуществления процесса отвода тепла. Ситуация недостатка жидкости в испарителе холодильной машины приводит к падению эффективности работы, а так же появлению условий эксплуатации выходящих за допустимы границы. Первым что необходимо отметить, что при снижении рабочего давления (температуры) кипения, происходит негативное изменение ряда ключевых параметров работы компрессора. Происходит рост температуры всасывания, что приводит к росту температуры нагнетания, а как следствие к перегреву компрессора и масла. Падение плотности пара на всасывании компрессора, а так же повышению степени сжатия компрессора, которая увеличивает перетечки и утечки пара внутри органов сжатия компрессора. Повышение степени сжатия, вызванное снижением вплоть до 0 рабочего давления всасывания, приводит к интенсивному росту температуры нагнетания компрессора, что в сумме с перетечками приводит к постоянному его перегреву. Однако, скрытность этого разрушения, связанного с перегревом, приводит к тому, что действие его происходит длительное время.
Низкий перегрев пара на всасывании компрессора Bitzer 4FE
Низкий перегрев пара на всасывании компрессора Bitzer CSH 85
Низкий перегрев пара на всасывании компрессора J& EHall HSM 3218
Низкий перегрев пара на всасывании компрессора Dorin H7500
Группа 5. Вспомагательное оборудование
Всомагательным оборудованием холодильной установки, являются элементы, не обеспечивающие напрямую реализацию процесса переноса тепла, а применяемые для повышения качественных характеристик установок и её компонентов. Также большое количество вспомагательных устройств обеспечивают повышение уровня надёжности основных компонентов установки. Среди оснвного оборудования, можно выделить несколько групп:
1. Объёмные аппарты
2. Устройтва сепарации
3. Запорная арматура, ручная/автоматическая
4. Запорно-регулирующая арматура
5. Клапаны направления потока
6. Системы поддержания давления
7. Системы поддержания температуры
8. Системы поддержания уровня
9. Прочее вспомагательное оборудование
Группа 6. Контрольно-измерительное оборудование
Часто АСУ ошибается по причине высоких погрешностей измерения, вязванных дефектами или особенностями установки КИПиА.
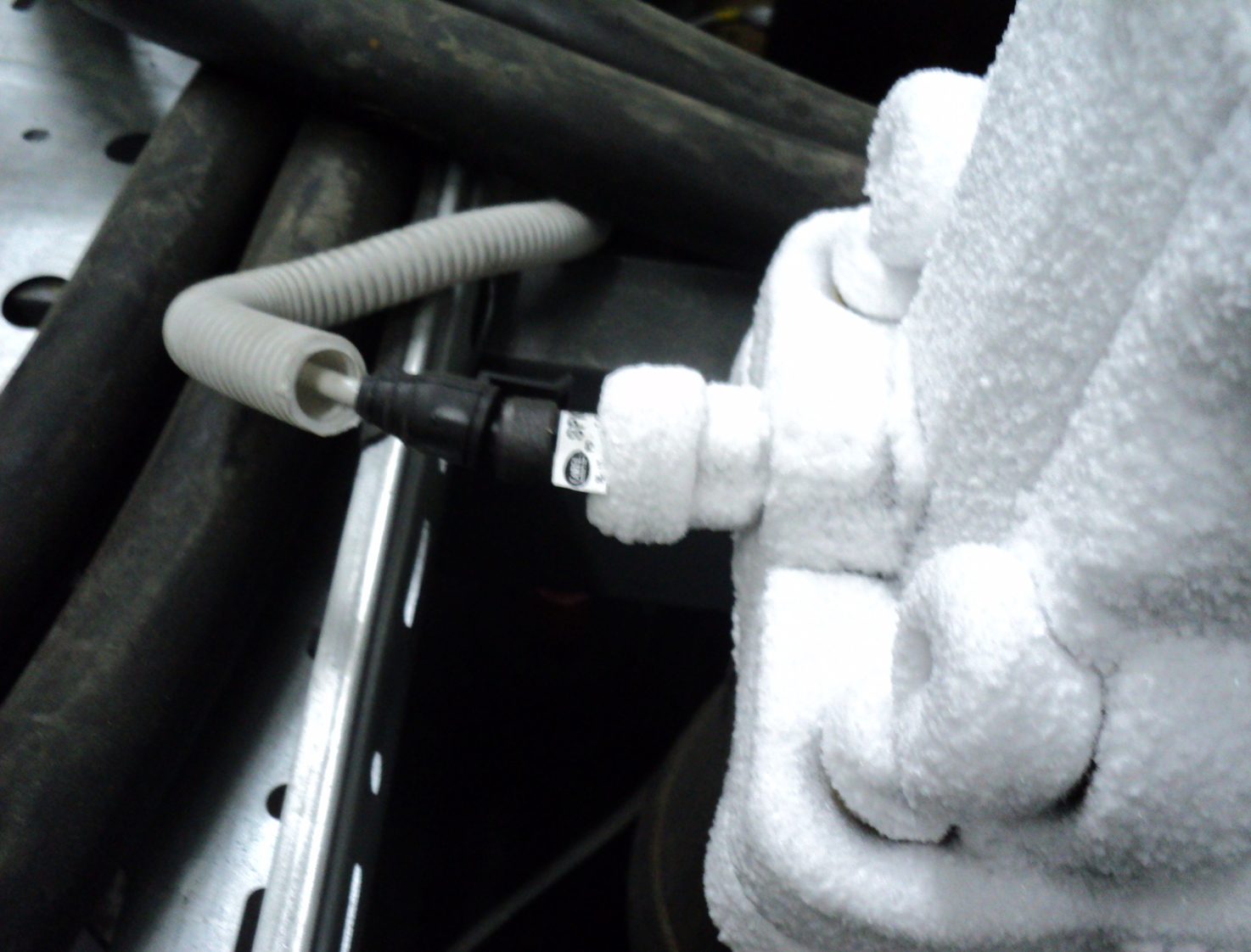
Некорректное положение датчика температуры масла после смешения
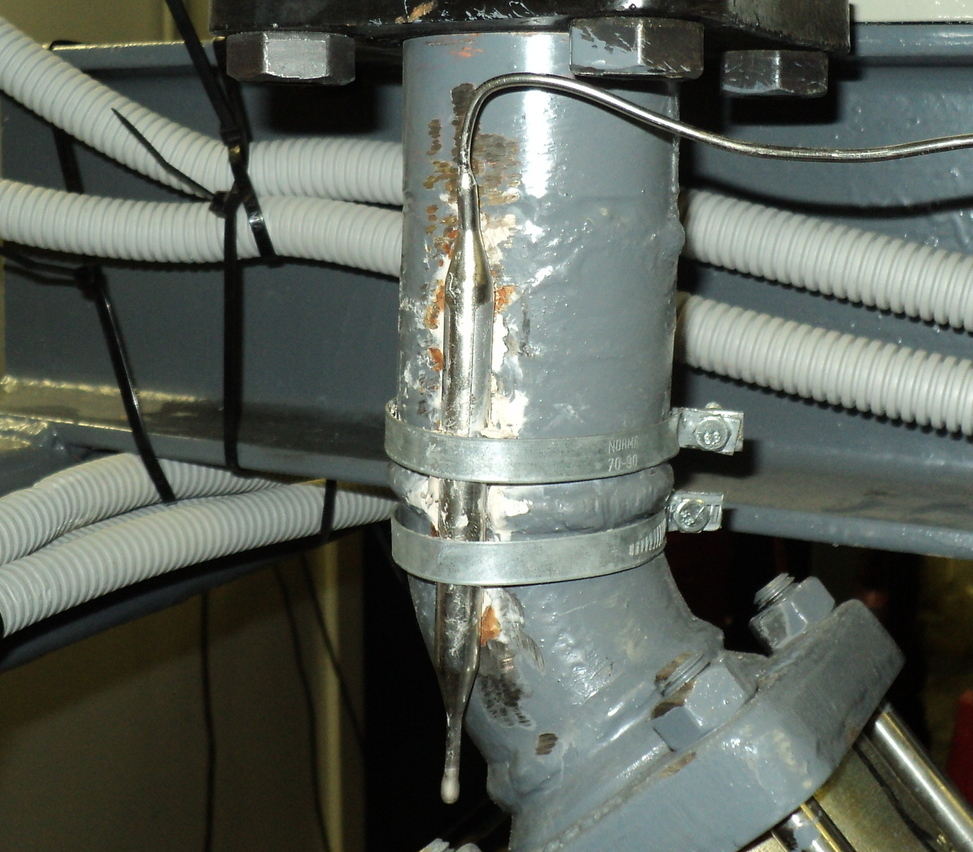
Некачественная установка термобаллона ТРВ Экономайзера
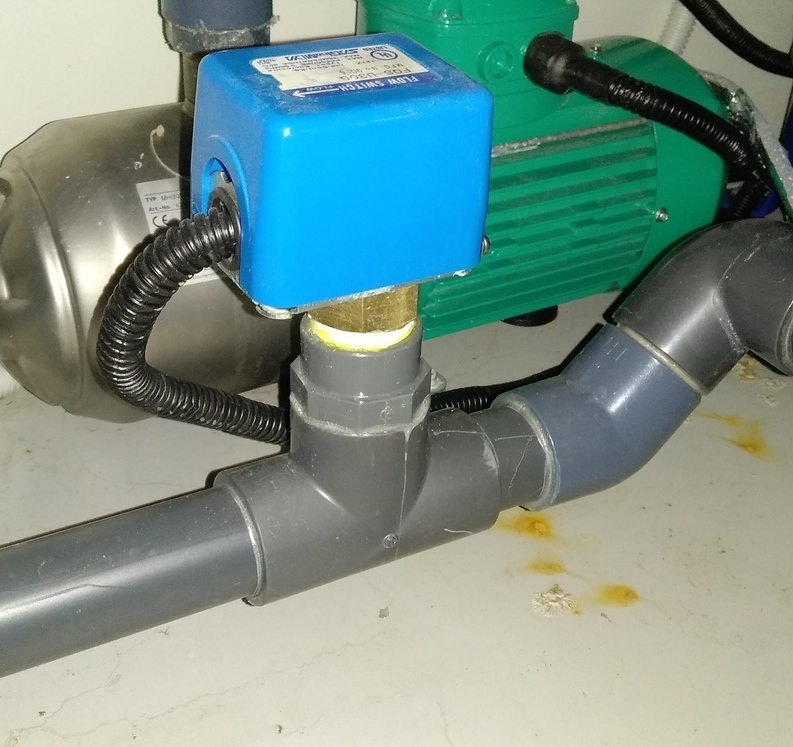
Дефект установки датчика температуры нагнетания
Датчик постоянно замерзает на линии всасывания из отделителя жидкости
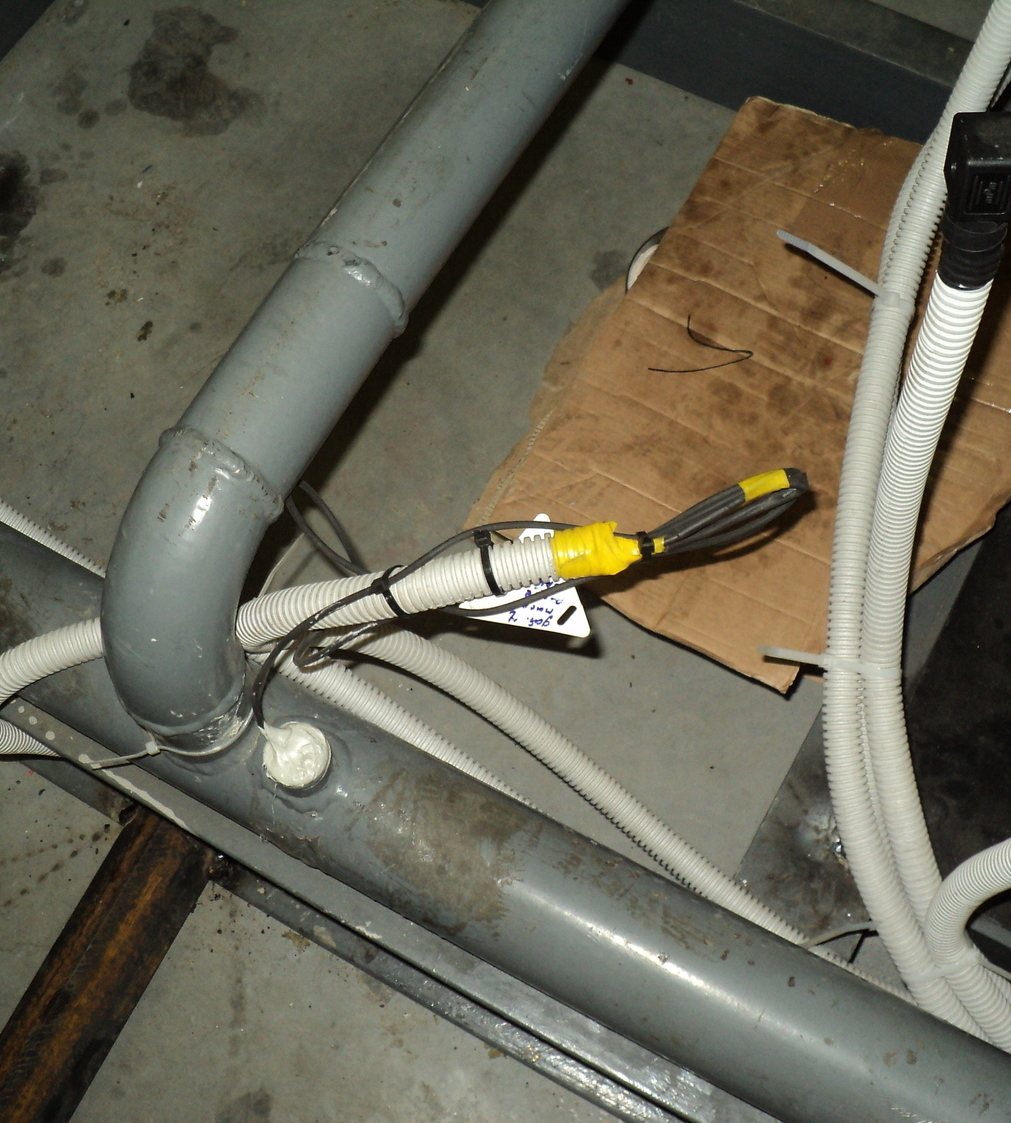
Дефект установки чуствительного элемента вентиля впрыска жидкости
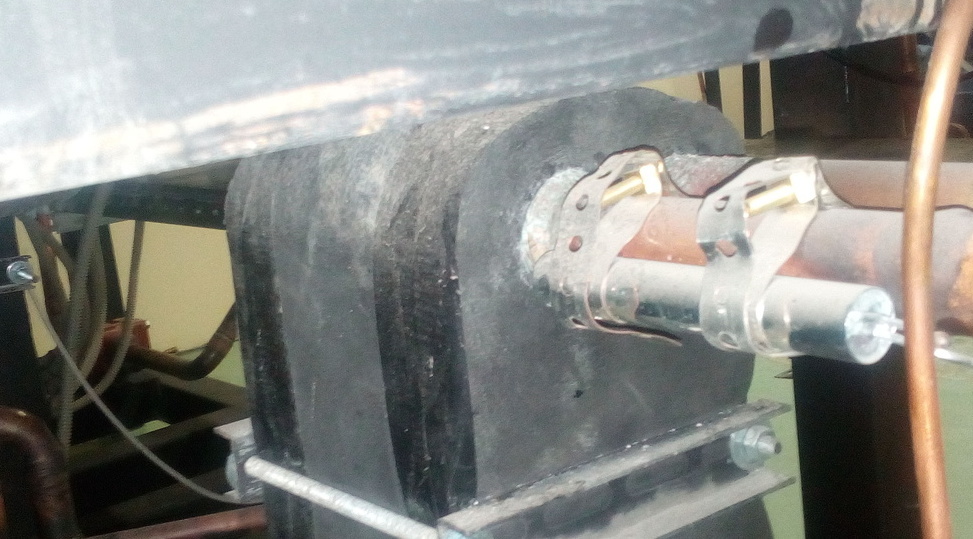
Дефект установки реле протока жидкости
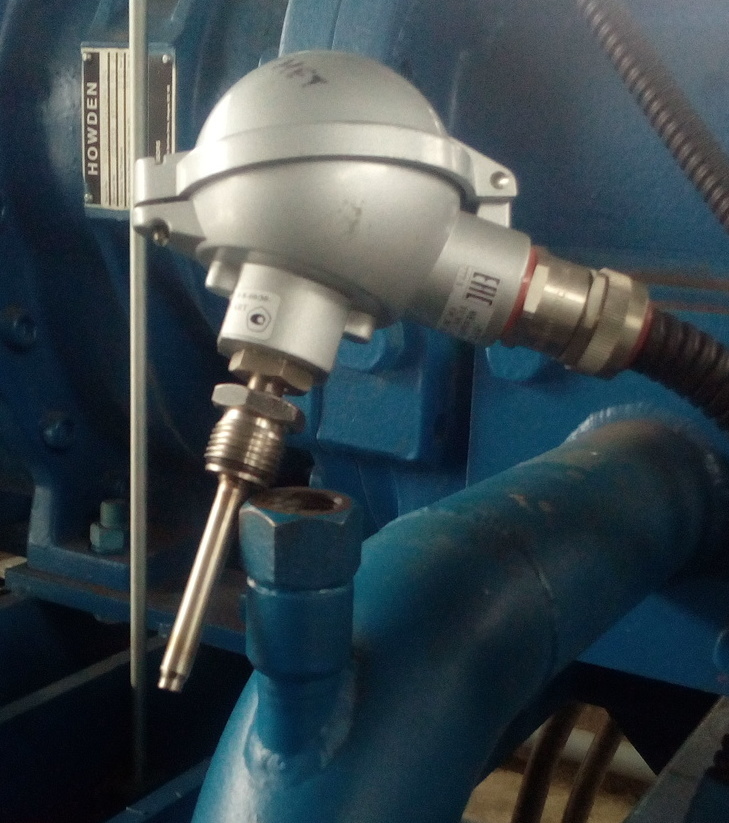
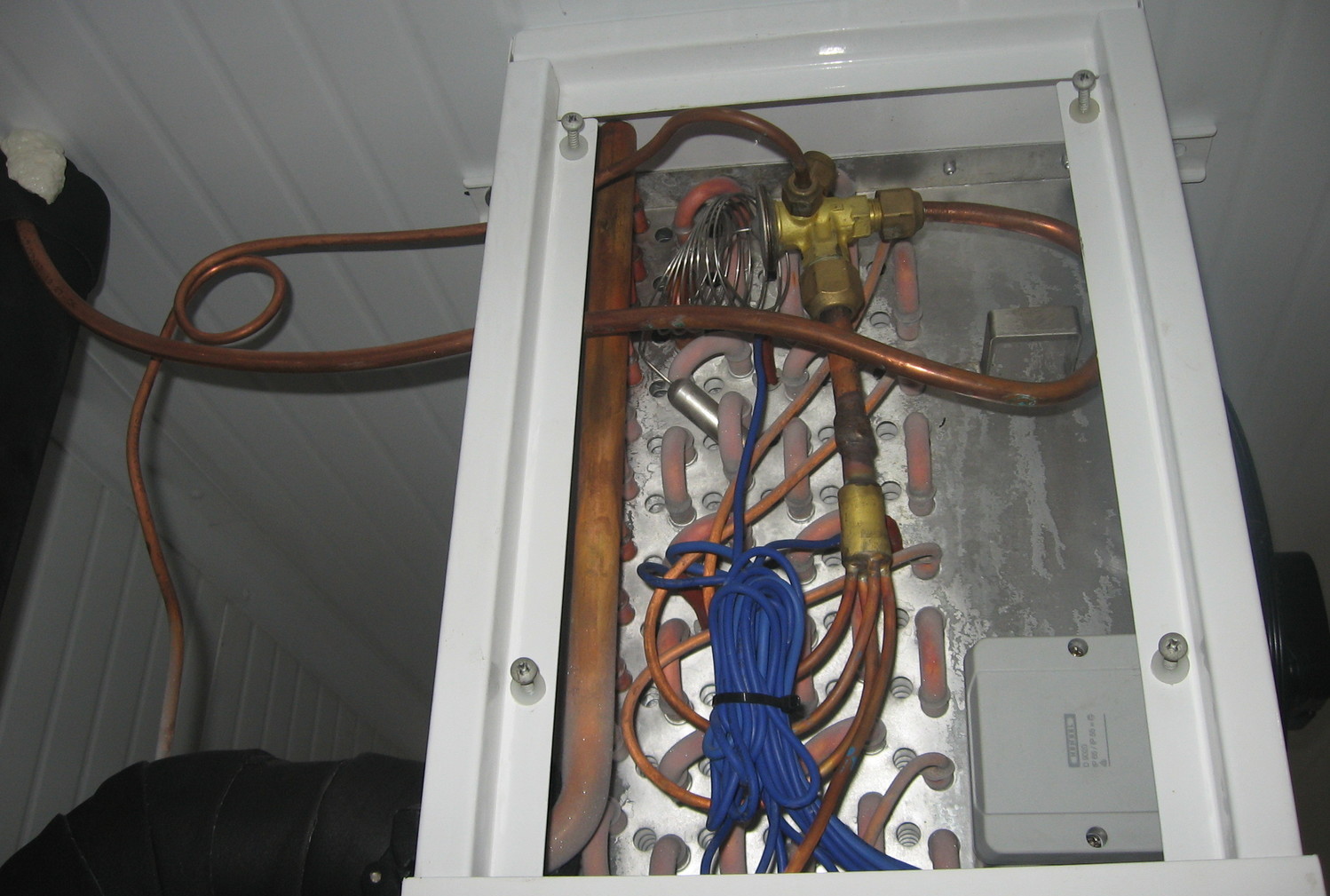
Типичная картина установки термобаллона ТРВ