Обслуживание и ремонт чиллеров. Охлаждение жидкостей
Охлаждение жидкости, одно из самых востребованных направлений применения холодильных машин. Использование промежуточных хладоносителей, делает возможным обеспечивать большую централизацию процесса охлаждения, а также позволяет использовать аккумулирующую способность контура хладоносителя, что в теории позволяет получить маскимально стабильную работу холодильной установки.
Компания EhS предлагает услуги по обслуживанию и ремонту промышленных охладителей жидкости различного назначения.
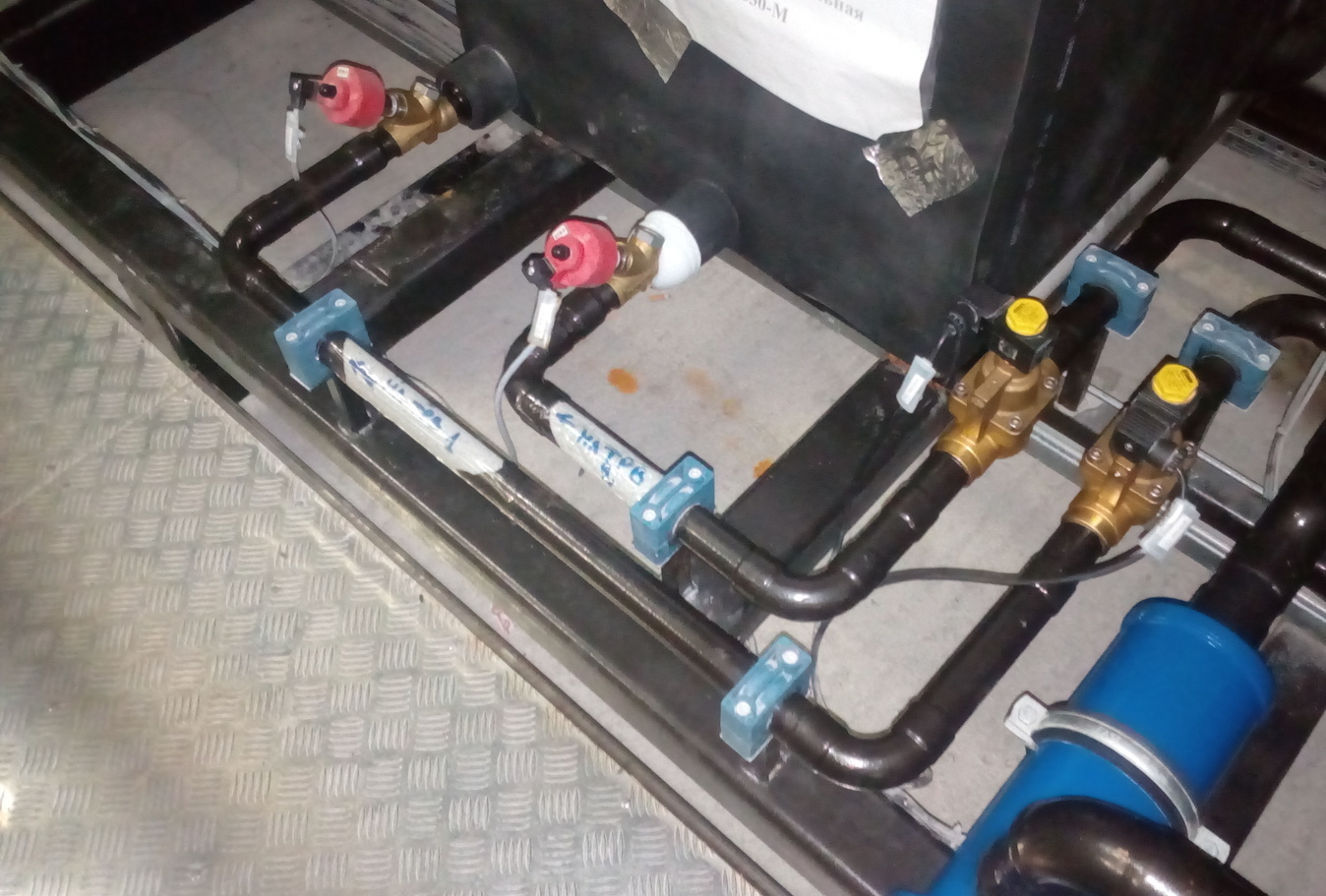
Перечень операций технического обслуживания чиллера, выполняемых компанией EhS.
БЛОЧНАЯ ХОЛОДИЛЬНАЯ МАШИНА
1. Визуальная проверка агрегата на наличие механических повреждений. Повреждения могут быть следствием как внешнего воздействия, так и внутреннего, связанного, например, с повышенной вибрацией отдельных элементов установки;
2. Визуальная проверка наличия утечек хладагента (теплоносителя) и масла. Как правило, масло является достаточно точным сигнализатором утечек хладагента, однако только проверка специализированным прибором может дать окончательный ответ. Нередко самым надёжным способом остаётся традиционное обмыливание;
3. Проверка давления в системе хладоносителя/теплоносителя. Совместно с этим процессом проверяется работа расширительного бака, а также контролируется работа дифференциального реле давления, если защита по потере потока реализована с его применением;
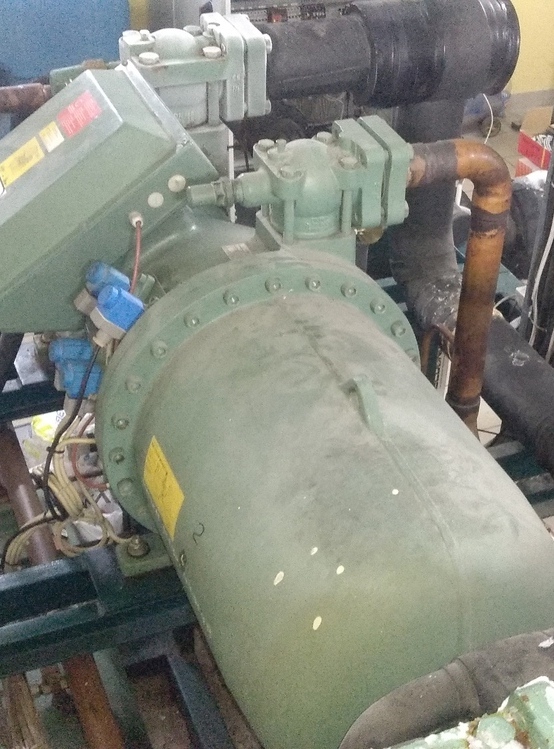
4. Проверка на наличие воздушных пробок в системе теплоносителя (при необходимости спуск, проверка работы воздухоотводчиков). Наличие воздушных или паровых пробок в системе снижает эффективность её работы, а также может привести к повреждению основных узлов.
! Критическое снижение давления, вкупе с неисправными системами спуска воздуха, могут привести к явлению кавитации, особенно в контуре теплоносителя.
5. Проверка надежности крепления элементов водоохлаждающей машины;
6. Занесение отчёта в журнал эксплуатации ХУ;
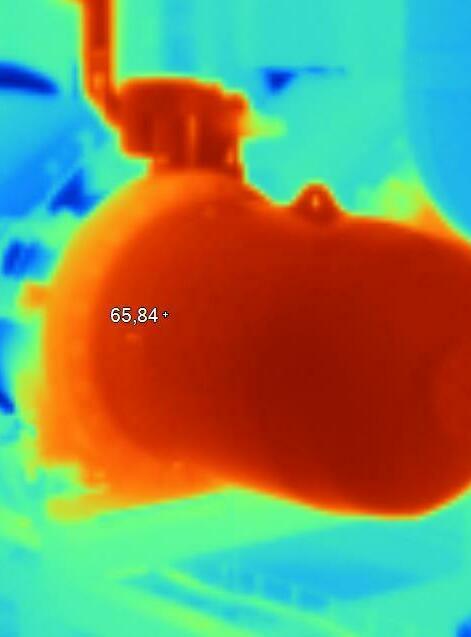
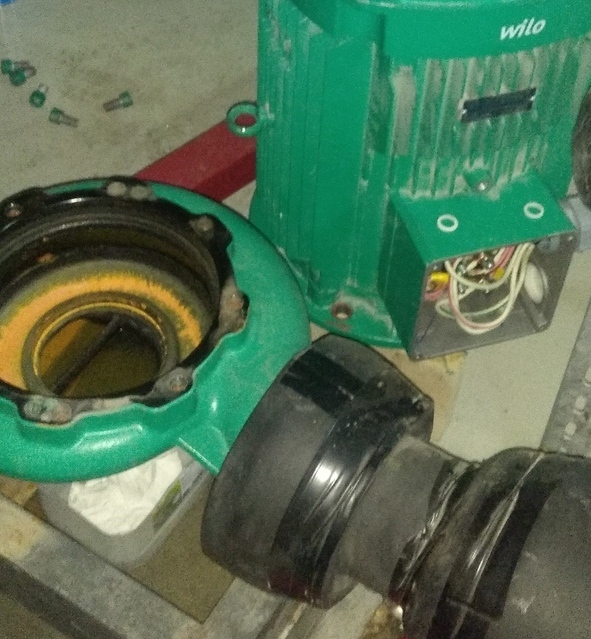
7. Проверка параметров работы установки, а также регулировка;
8. Создание и заполнение журнала эксплуатации;
9. Проверка подшипников на износ (общая вибрационная диагностика). Как правило, именно износ опор валов приводит к появлению излишней вибрации;
10. Проверка работы фильтра на всасывании. Чистка при необходимости;
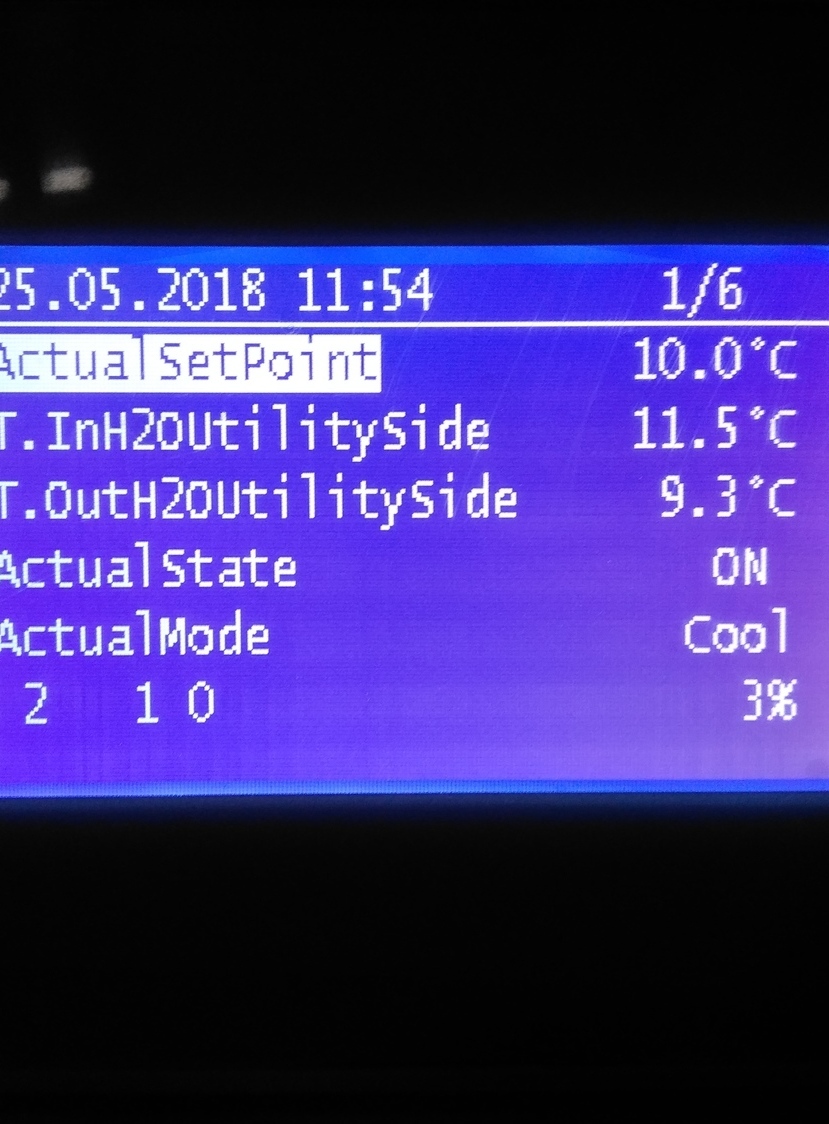
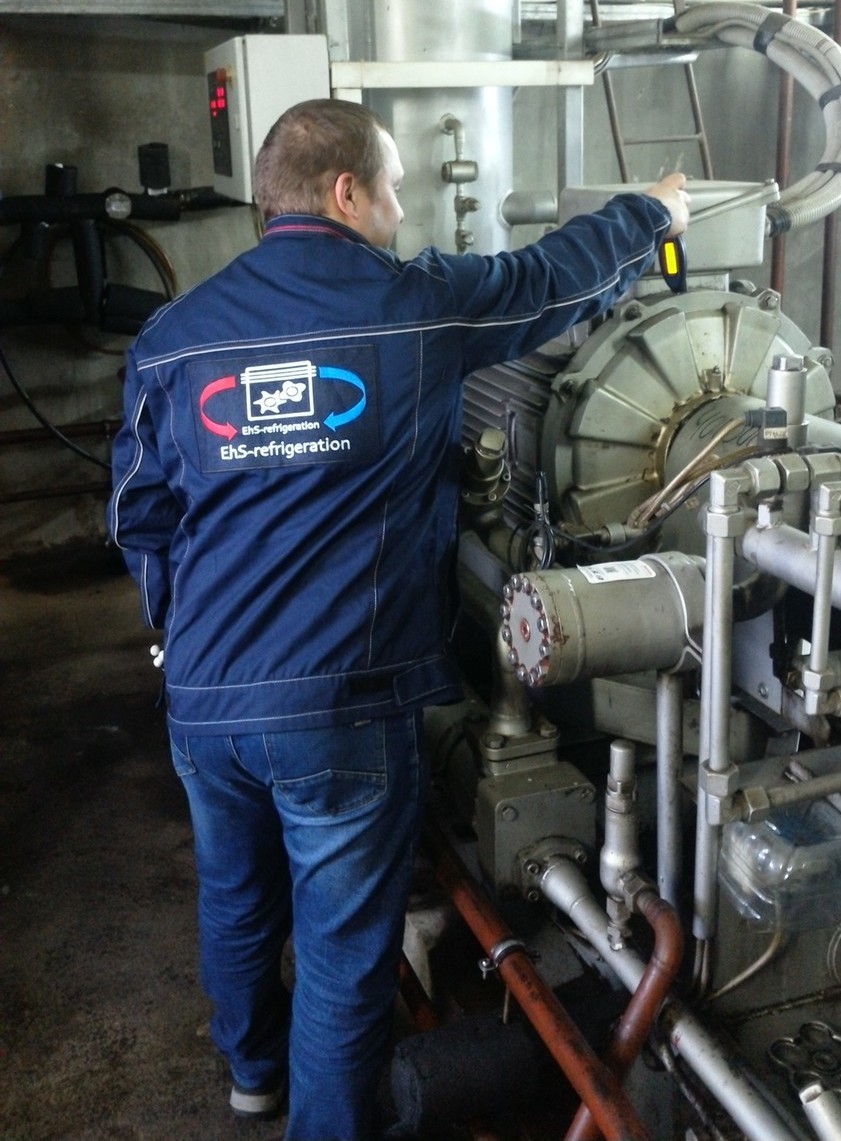
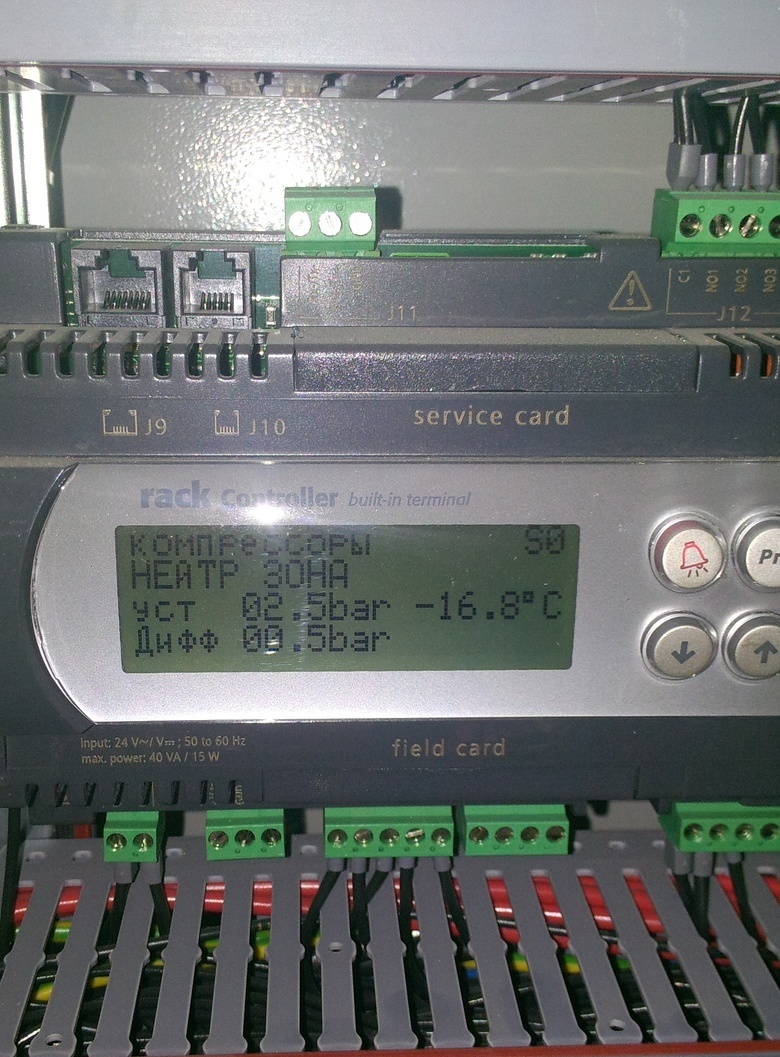
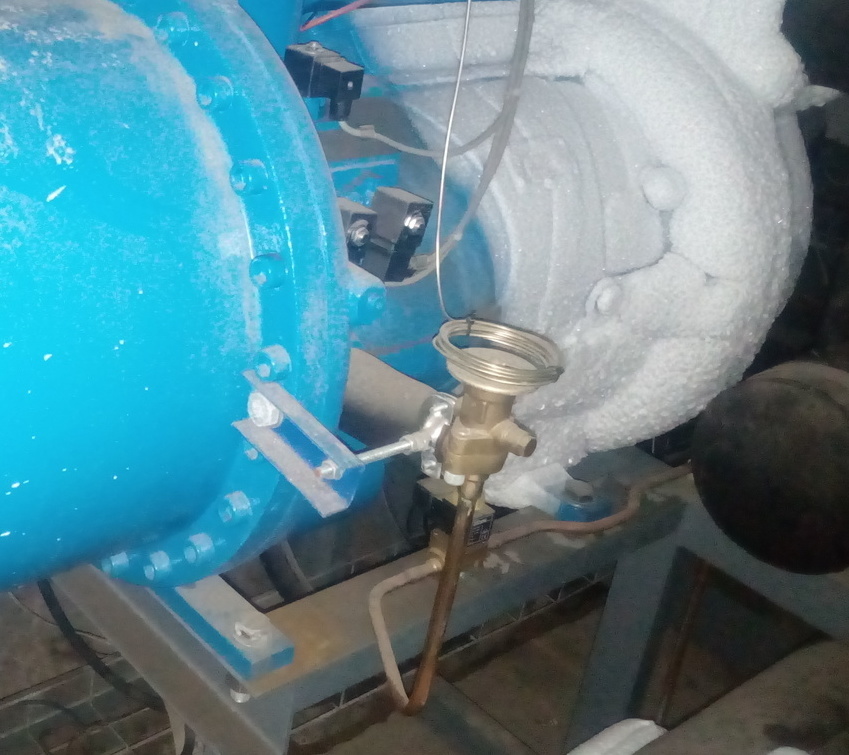
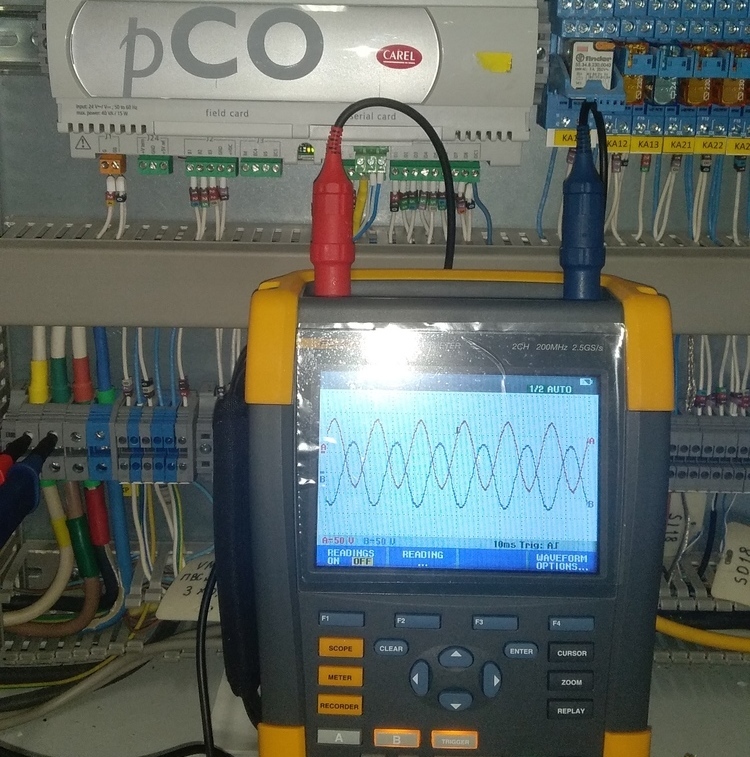
11. Настройка впрыска доохладителя (если установлен). Температурный уровень позволяет применять винтовые компрессоры без внешнего охлаждения масла, однако в редких случаях охлаждение всё же требуется, и задача решается впрыском жидкости в полость сжатия, что весьма эффективно, не допуская при этом перегрева рабочих органов компрессора;
12. Контроль загрузки электродвигателя компрессора. Оценка его эффективности. Контроль процесса сжатия. Оценка СОР;
13. Центровка и контроль положения дисковой муфты. В случае применения в составе компрессорного агрегата открытого компрессора;
14. Проверка и настройка системы естественного охлаждения (фрикулинг). Настройка смесительного клапана.
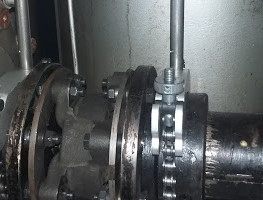
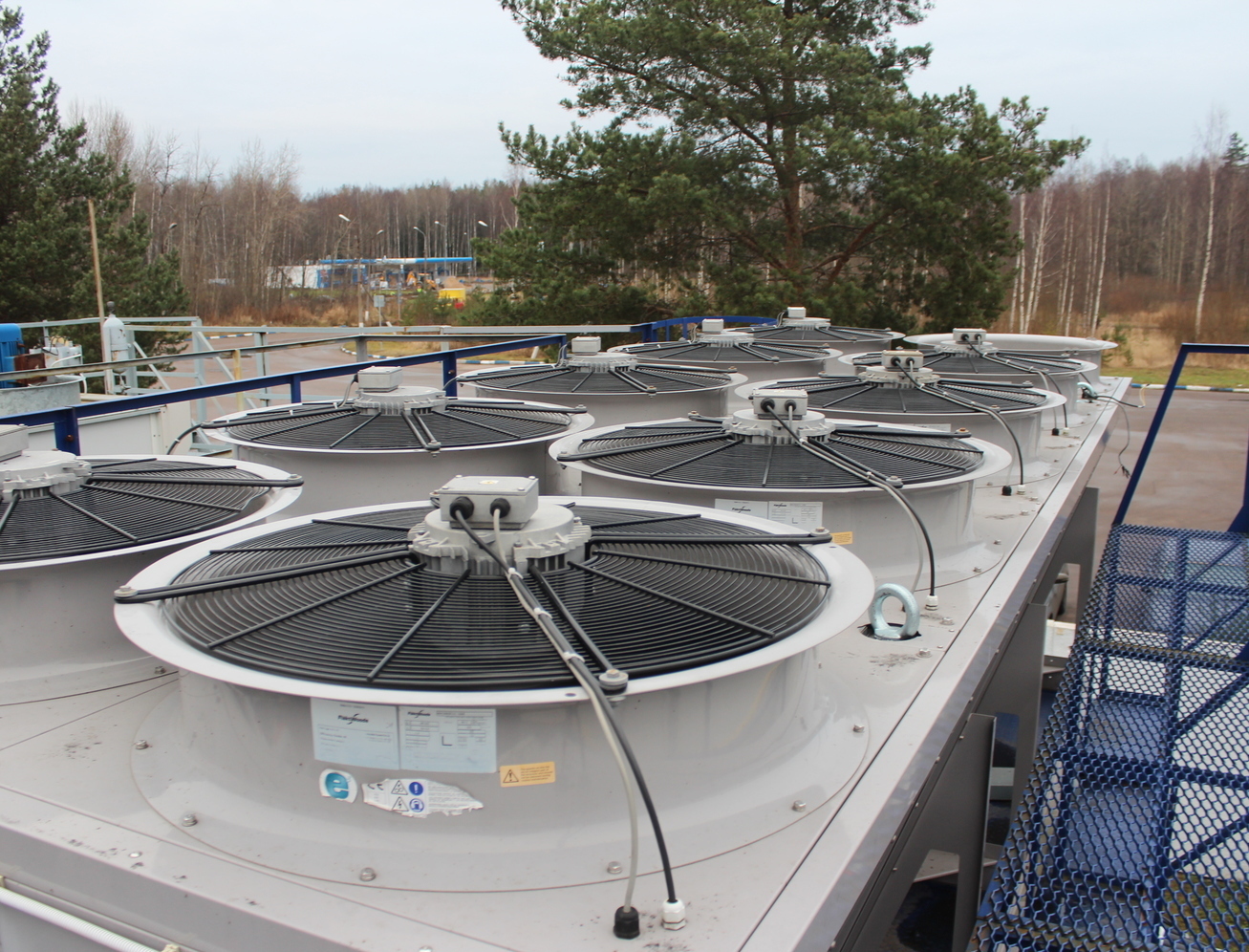
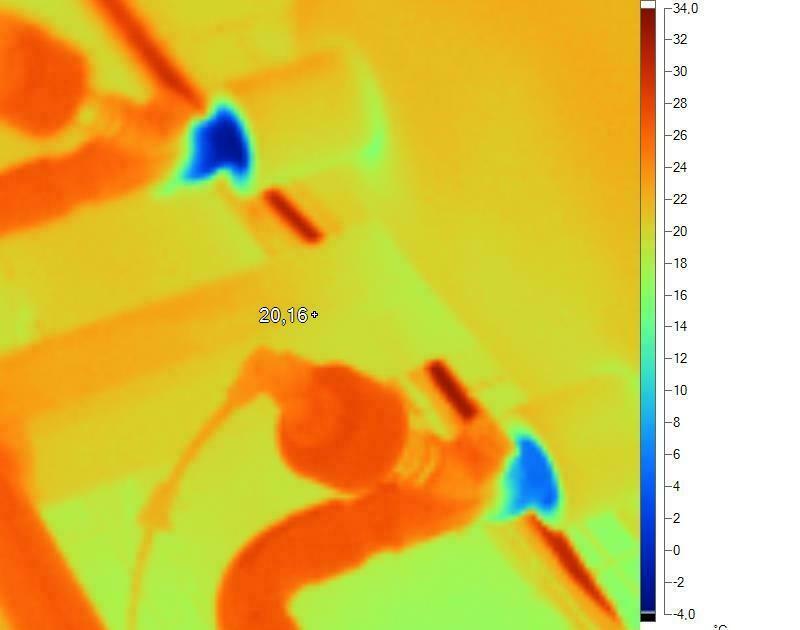
Охлаждающий контур
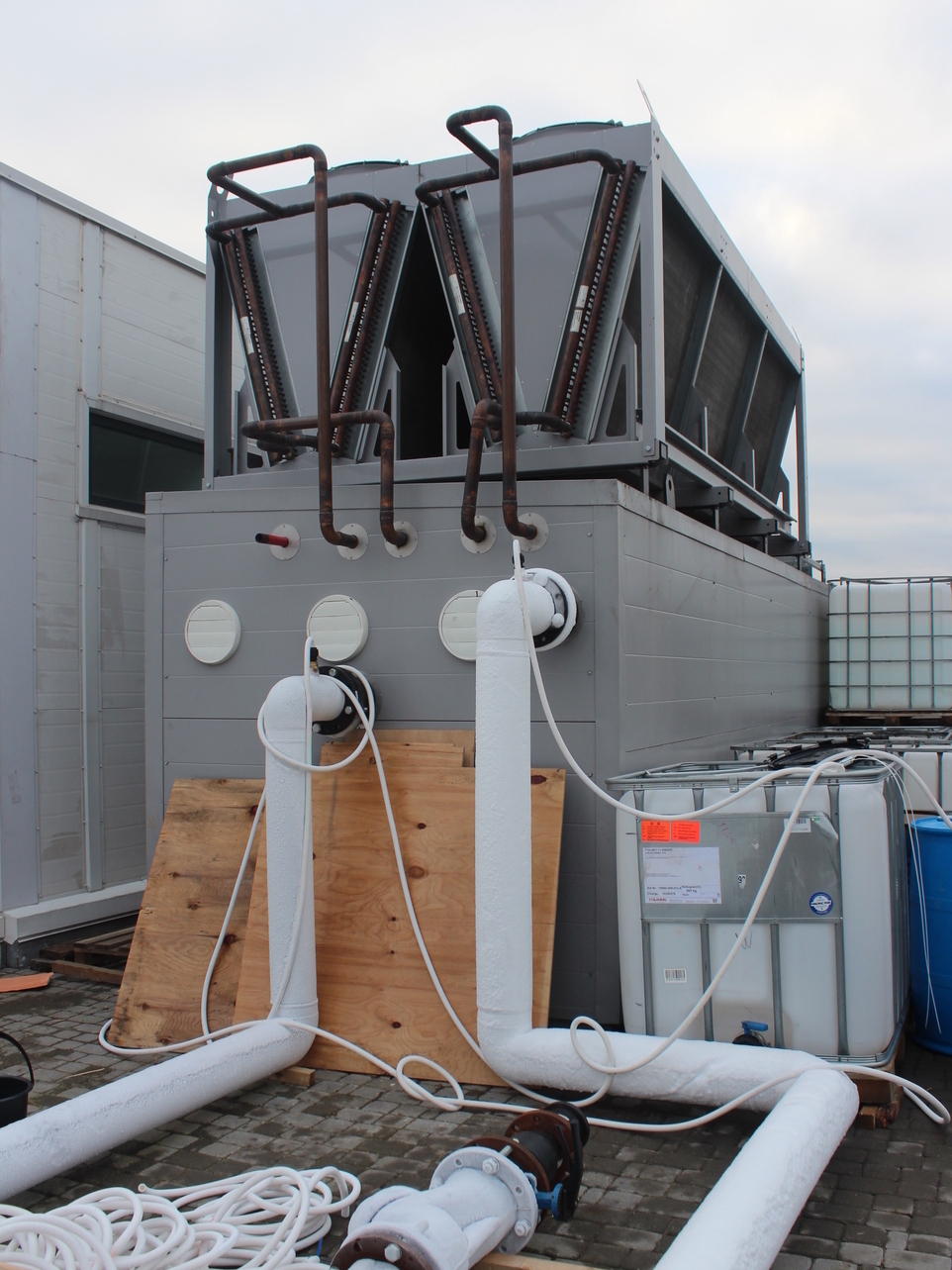
1. Проверка контура хладагента на отсутствие повреждений (утечек) специализированным прибором (в т.ч. мыльным раствором). Потеря рабочего вещества холодильным контуром приводит не просто к снижению энергетической эффективности установки в целом, но и к полной её остановке;
2. Проверка целостности теплоизоляционного слоя в меньшей степени влияет на энергоэффективность, однако ржавчина и плохой эстетический вид, сопровождающийся лужами под местами повреждения теплоизоляционного покрова, является следствием нарушения слоя теплоизоляции;
3. Проверка герметичности контура хдадоносителя;
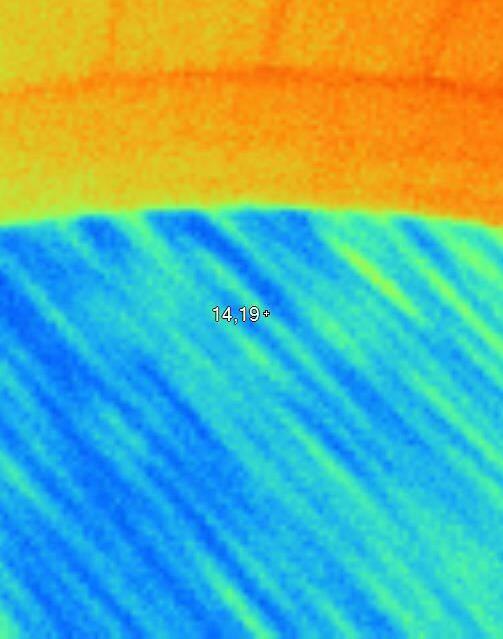
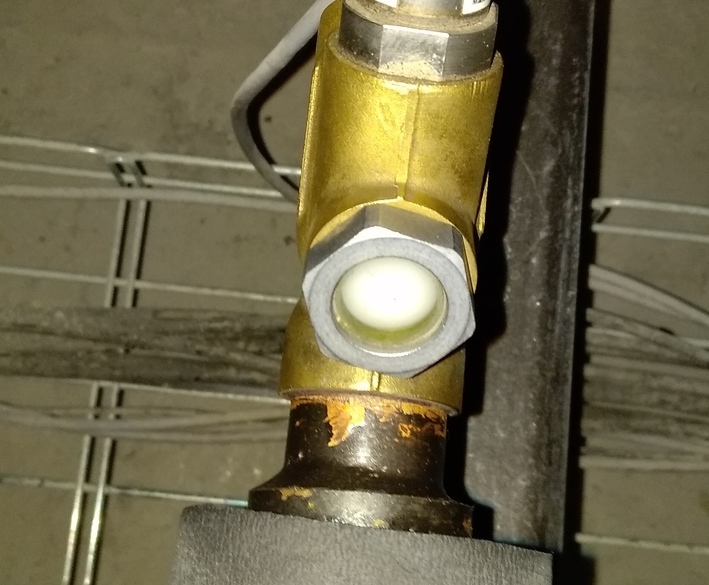
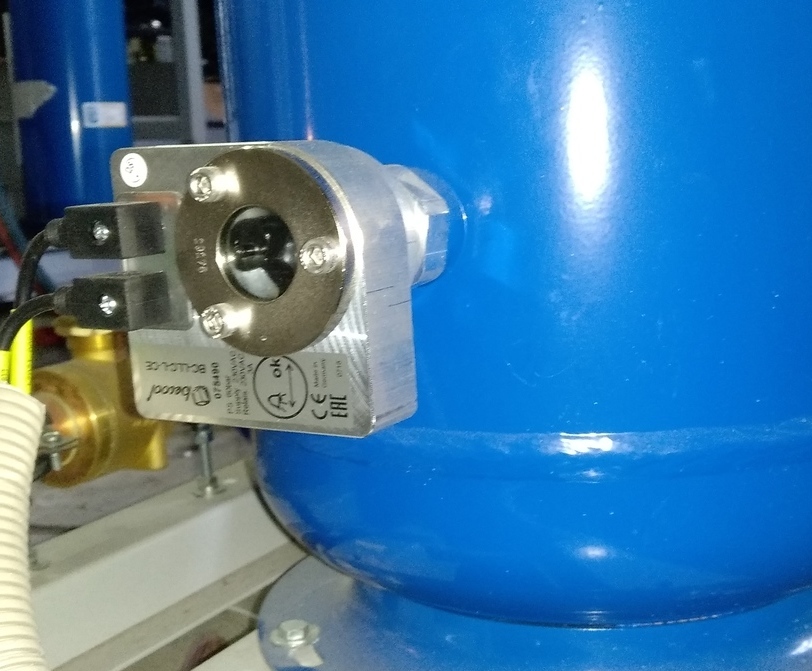
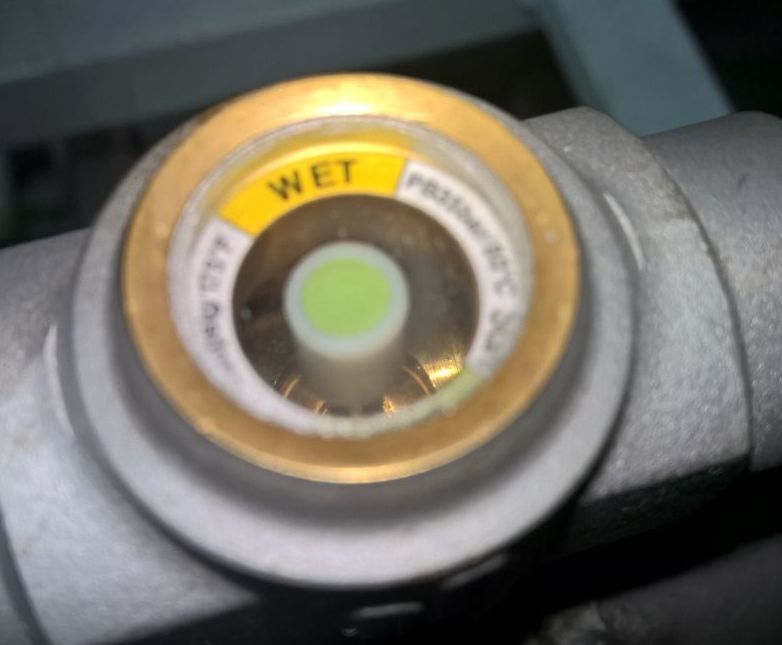
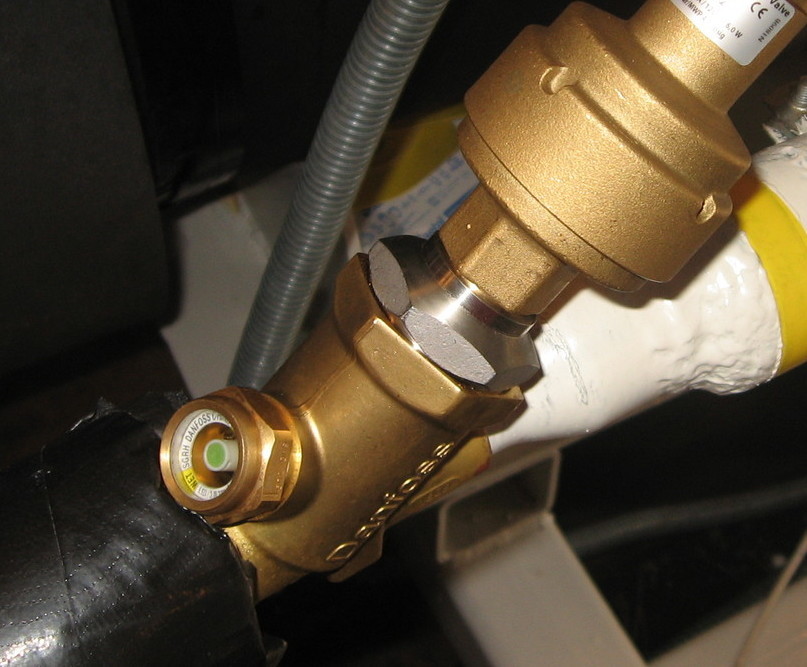
4. Проверка состояния потока в смотровом стекле жидкостного трубопровода. Также, но реже при использовании линейного ресивера оценить количество жидкости можно по мерной колонке или смотровым стёклам;
5. Проверка падения давления на фильтре жидкости, влажность в контуре;
6. Проверка индикатора влажности на изменение цвета. Достаточно частое явление после ПНР;
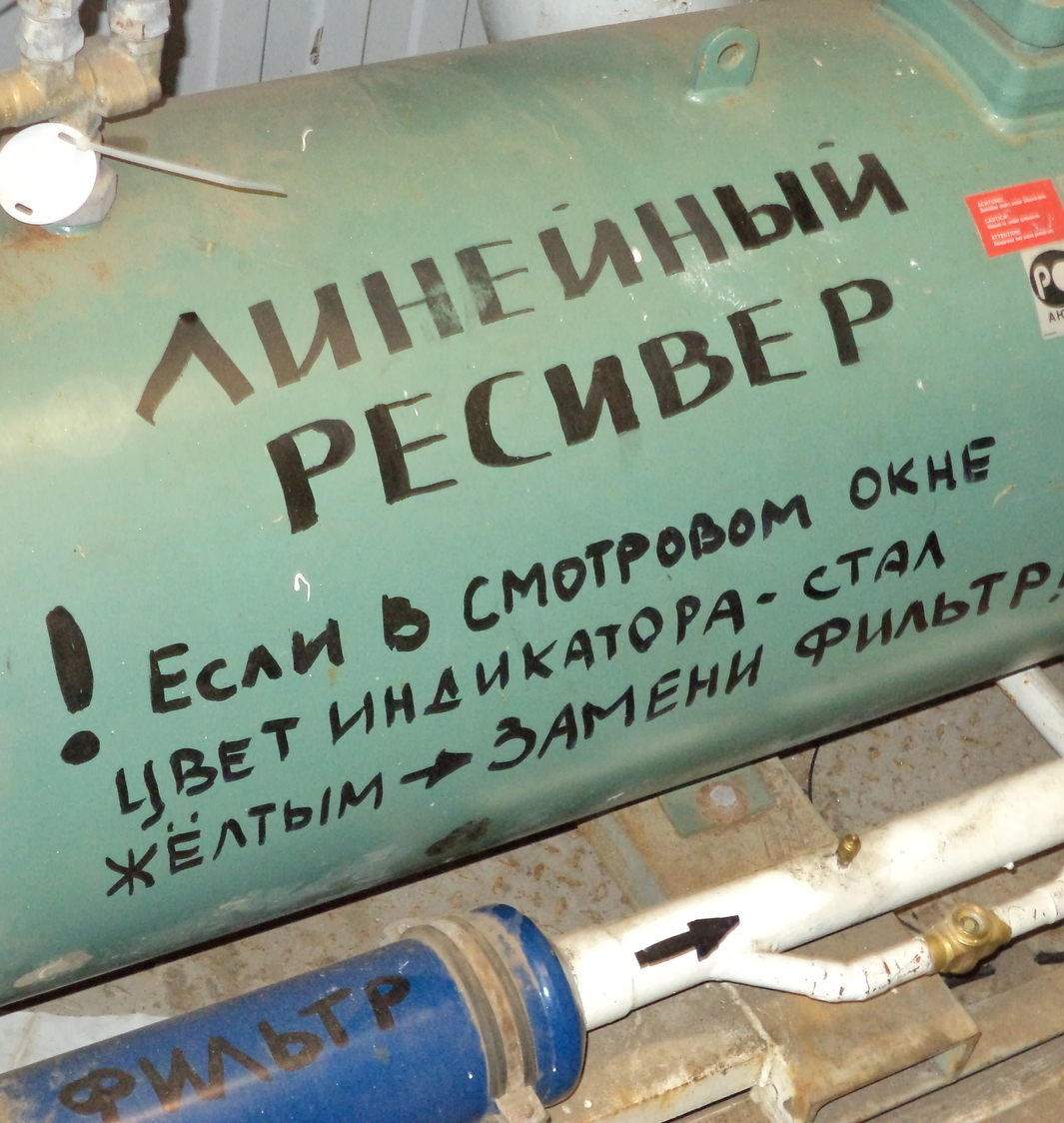
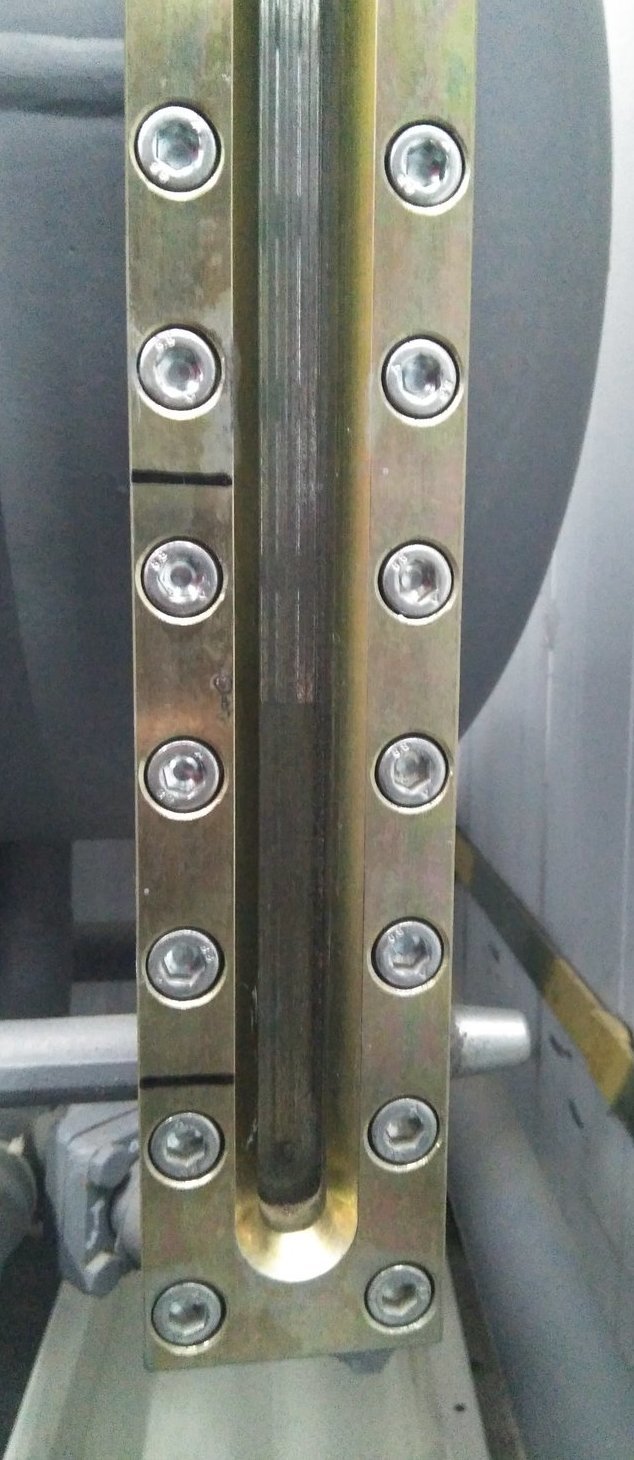
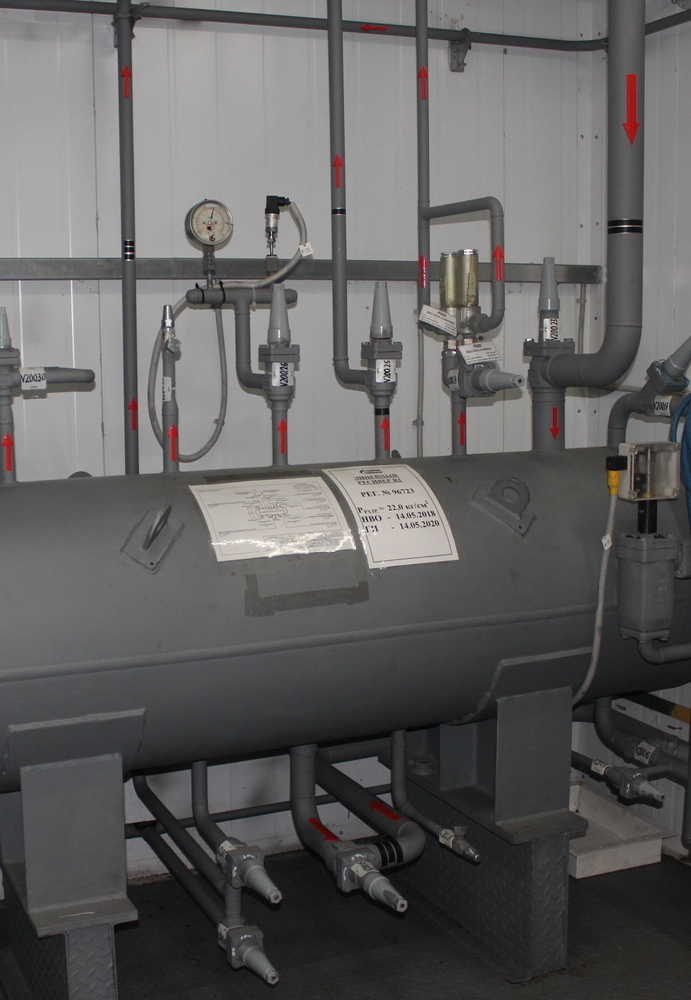
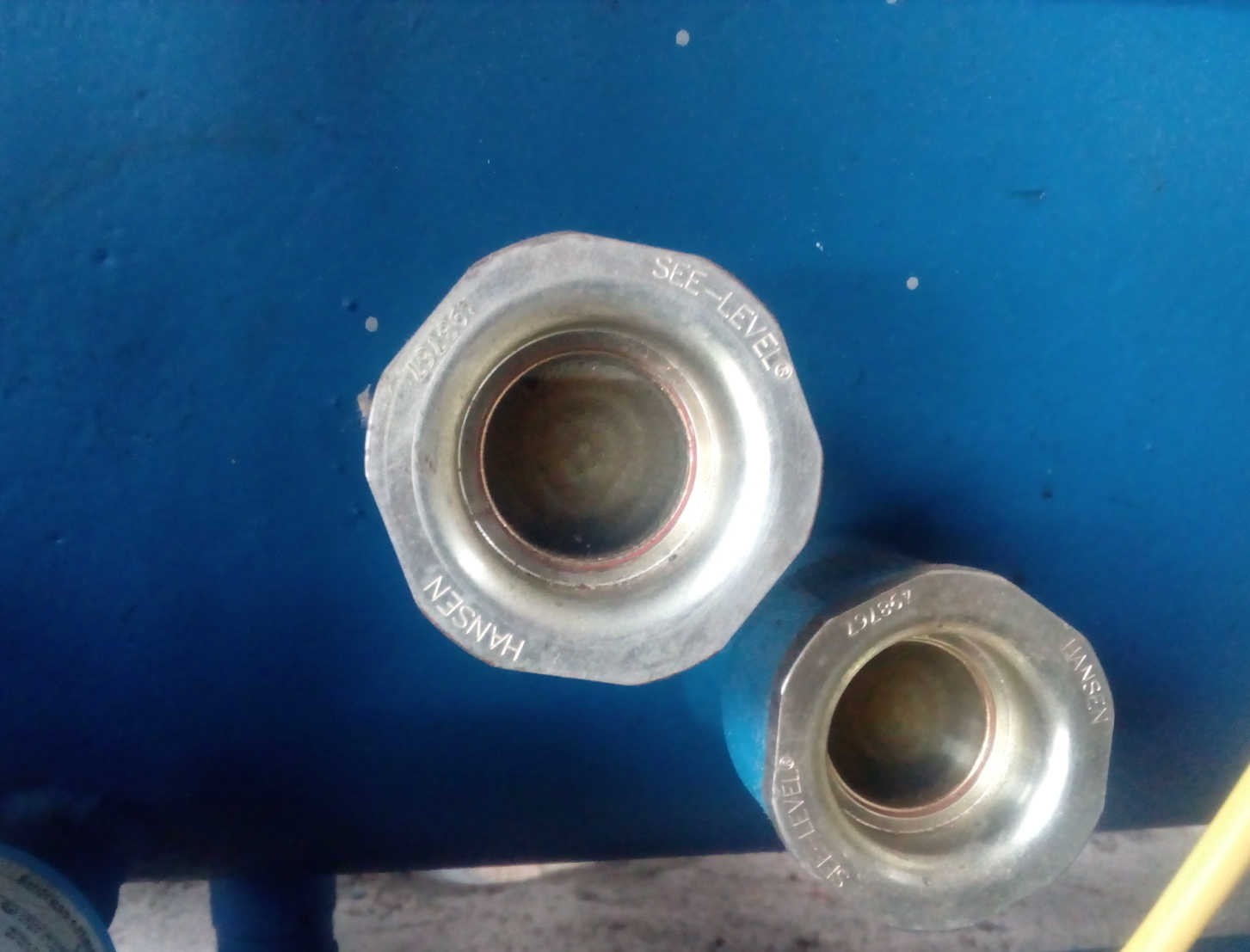
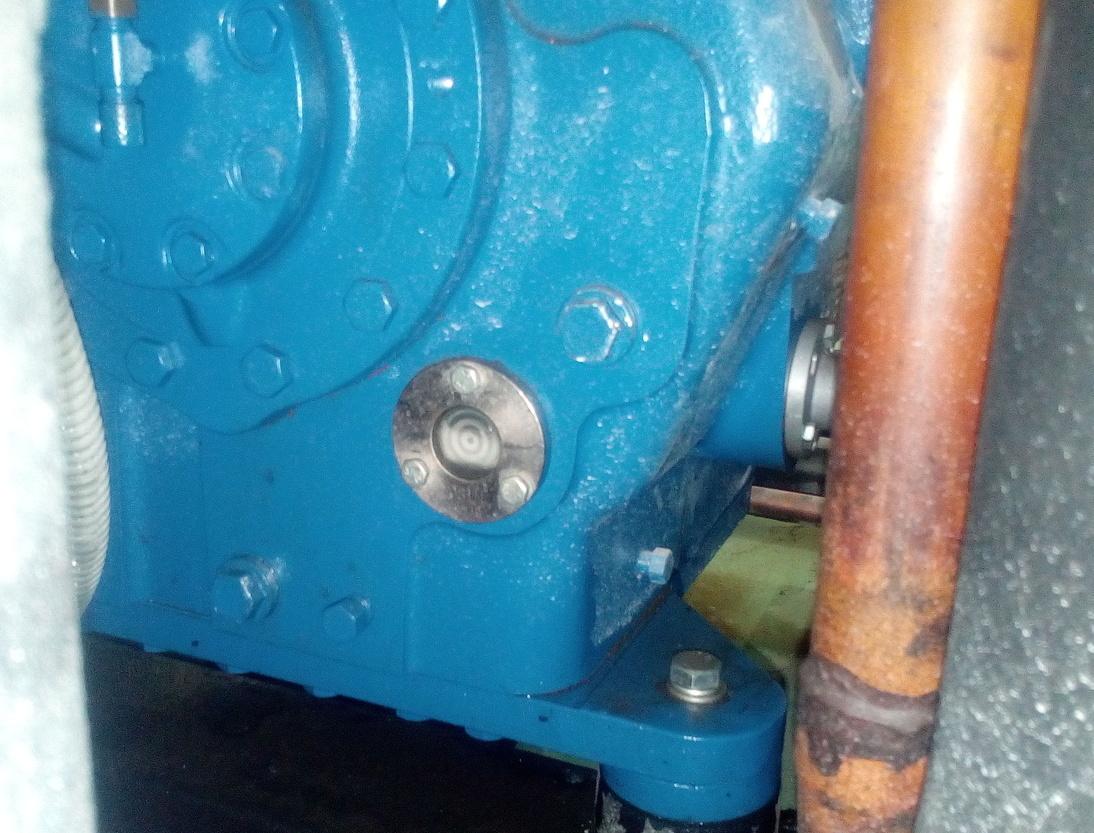
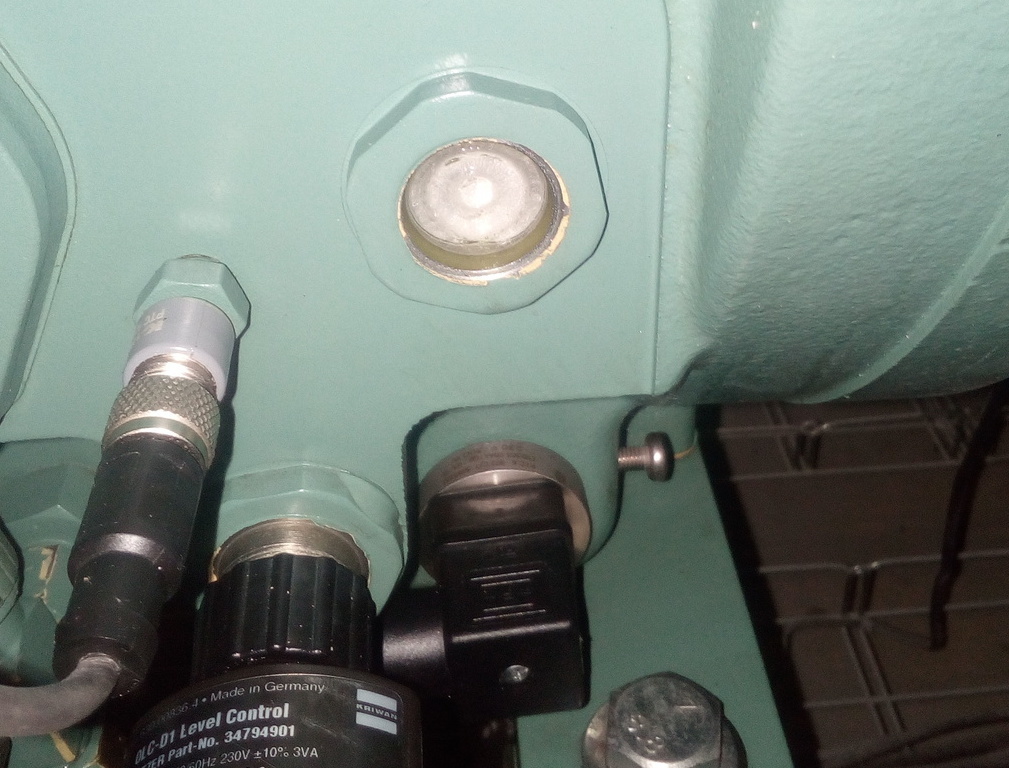
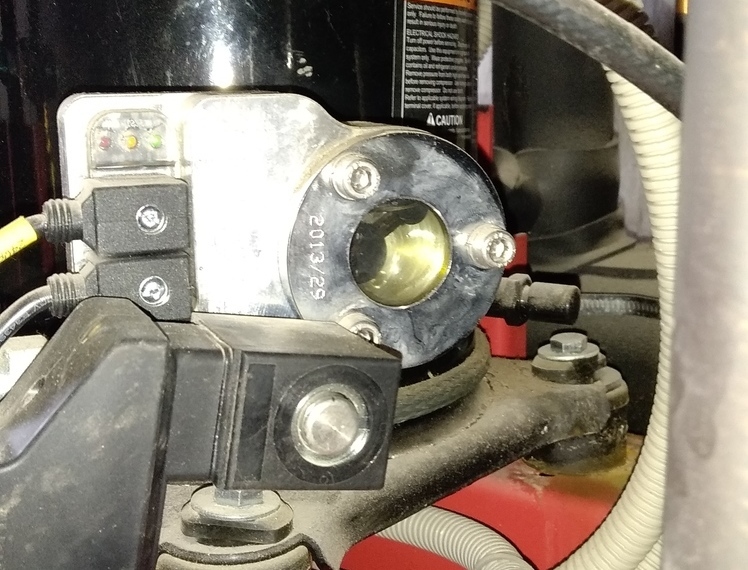
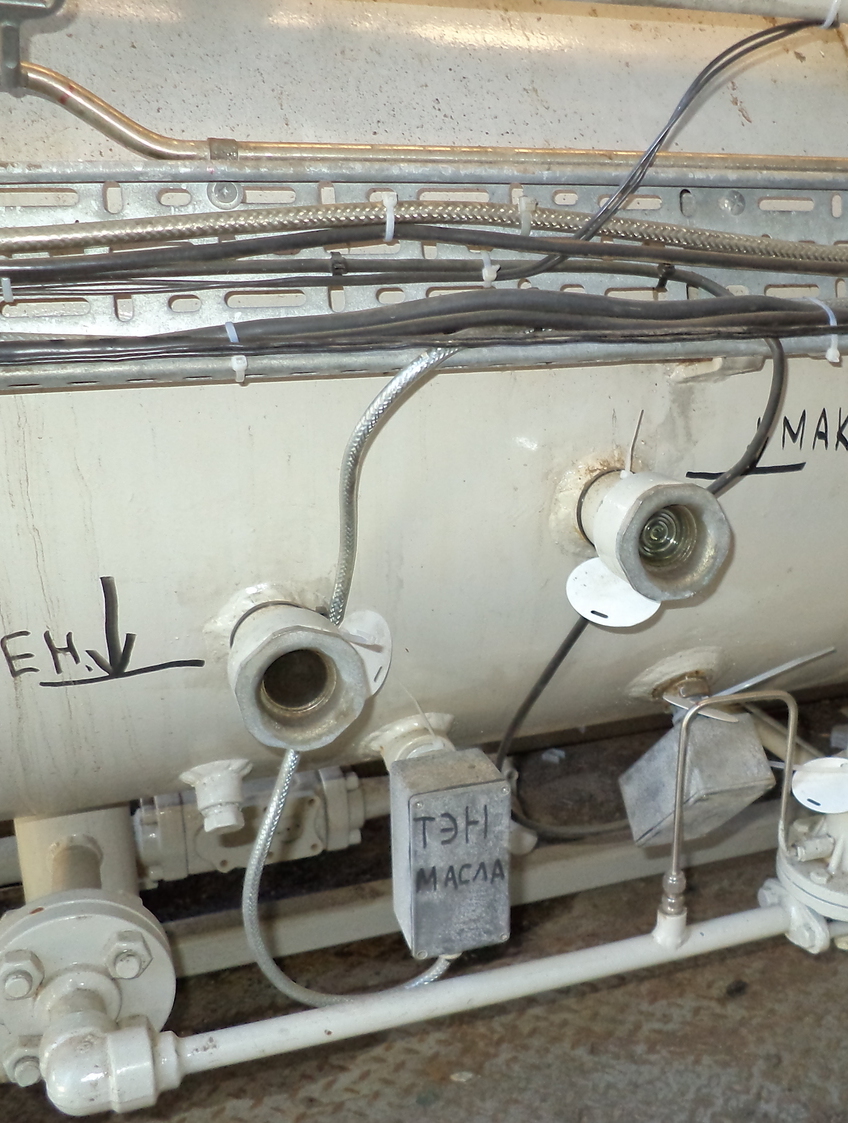
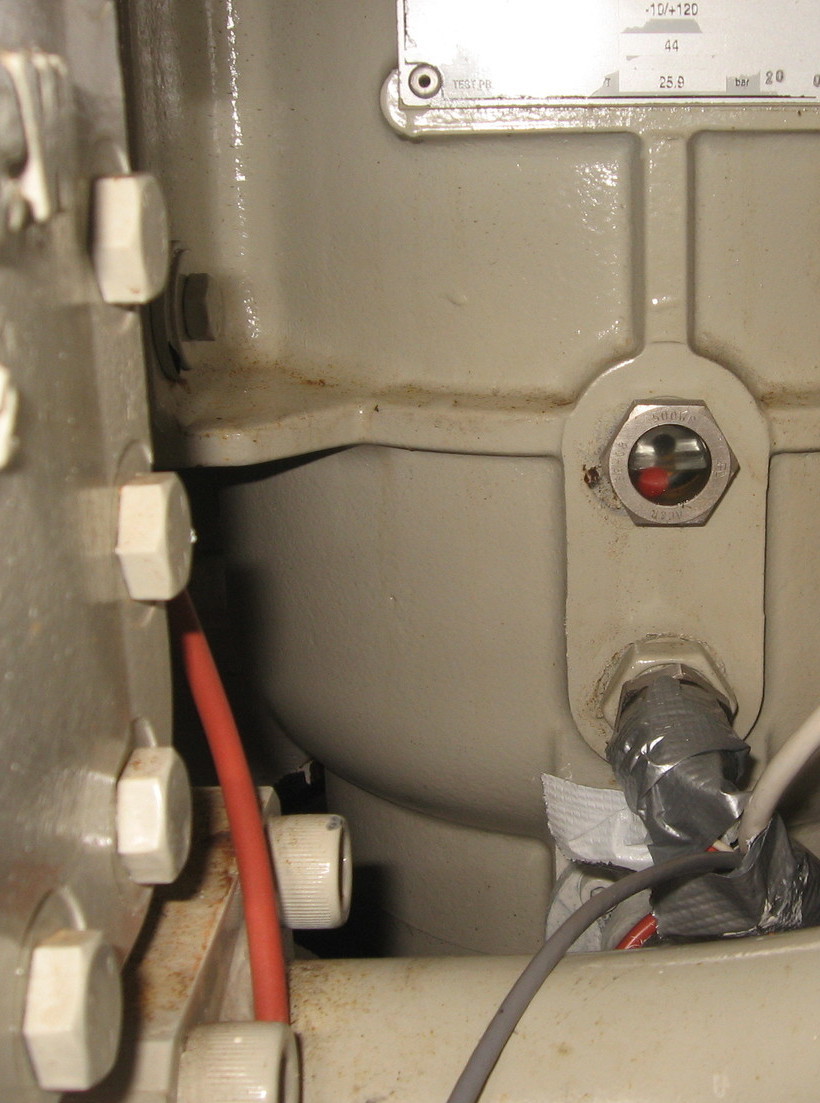
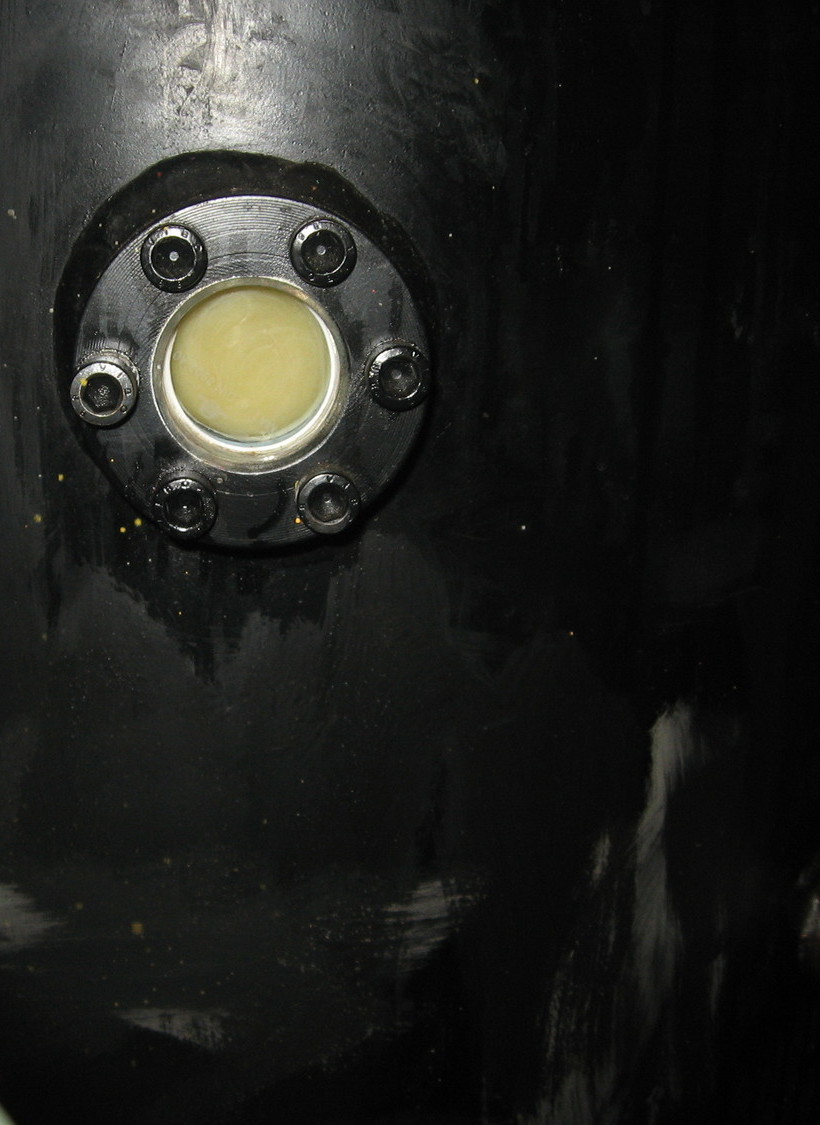
7. Проверка уровня масла в компрессоре и в отделителе масла (маслосборнике). Место контроля количества масла зависит от типа используемого компрессора, если у поршневых (спиральных) машин, как правило, уровень картеров компрессоров и маслосборник, то в случае винтовой машины уровень масла оценивается по уровню в отделителе, который зачастую является ещё и накопителем масла;
8. Проверка циркуляции масла в контуре, контроль работы ректификатора. Возврат масла из систем с отделителями жидкости, как правило, реализован с применением ректификационных систем. Режим работ такой системы прост и основан на разделении двух компонентов путём нагрева смеси. Но отбор смеси может происходить разными способами, и многие из них требуют регулировки и обслуживания;
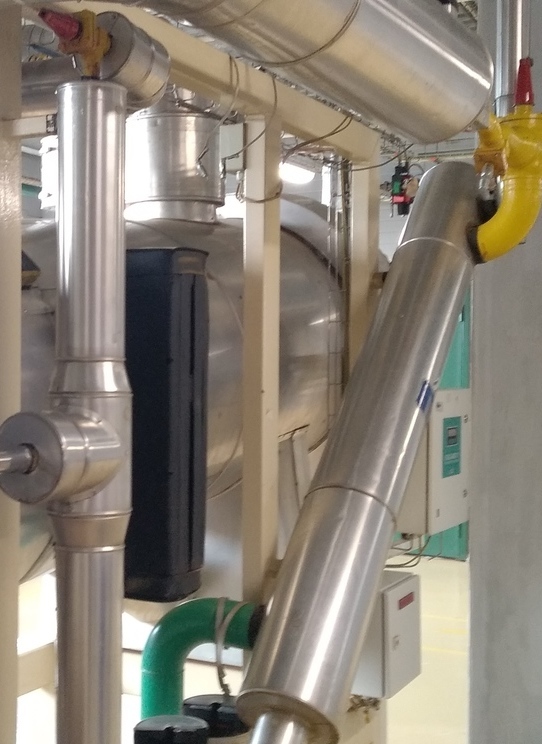
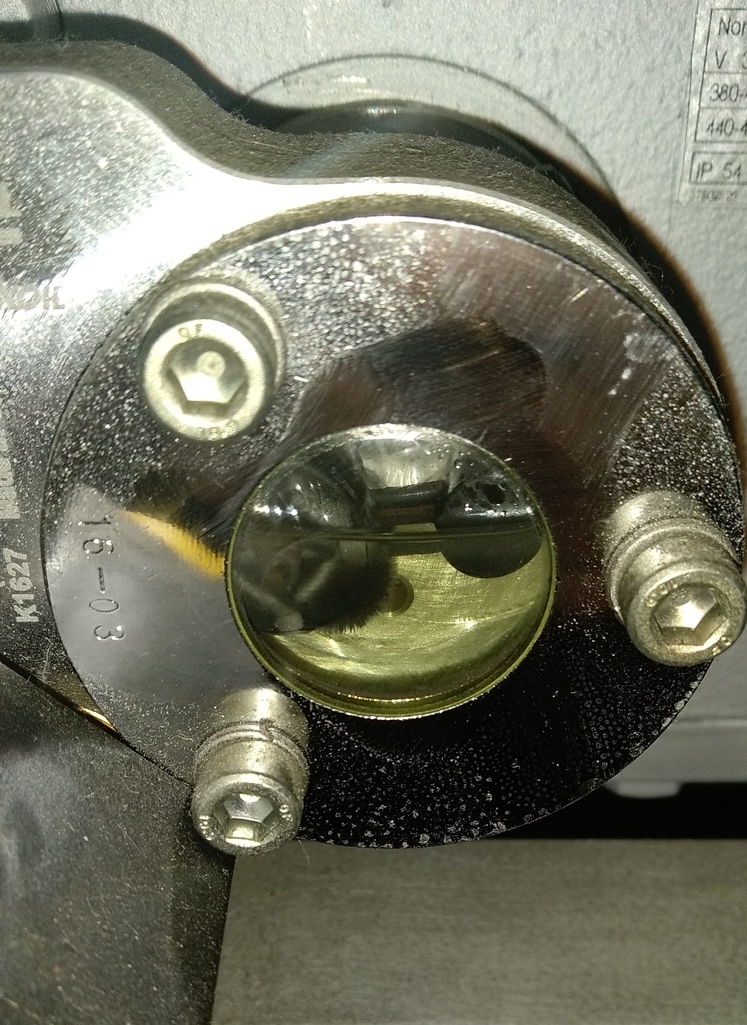
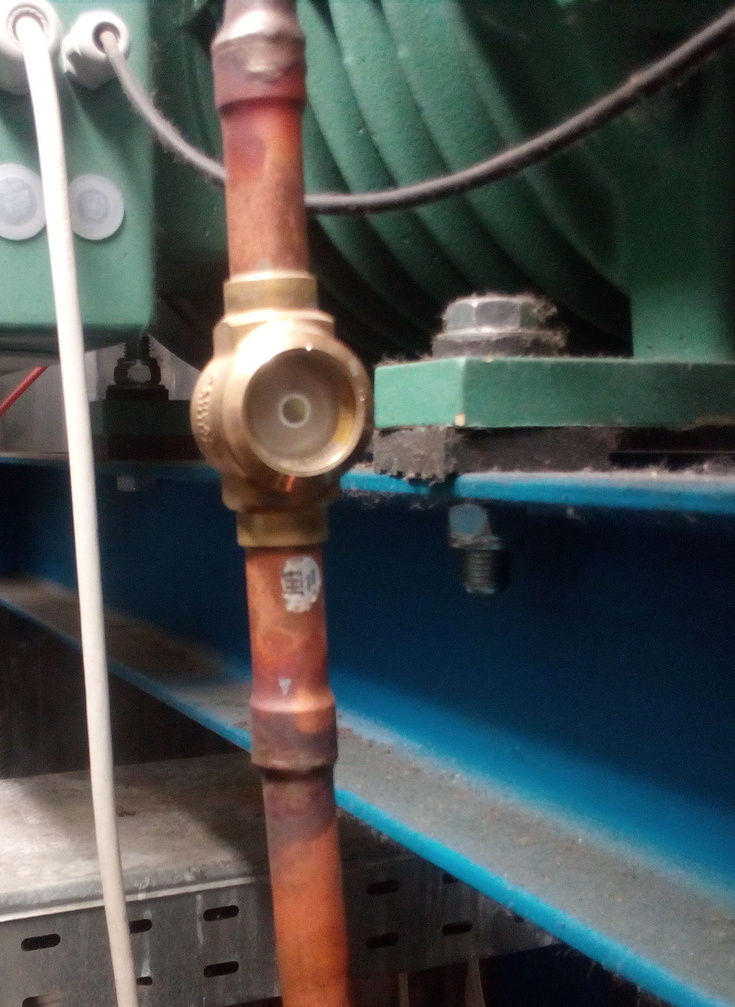
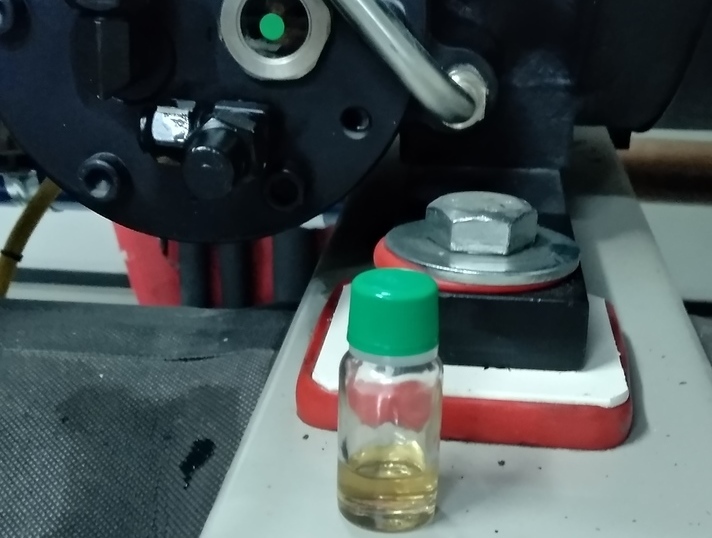
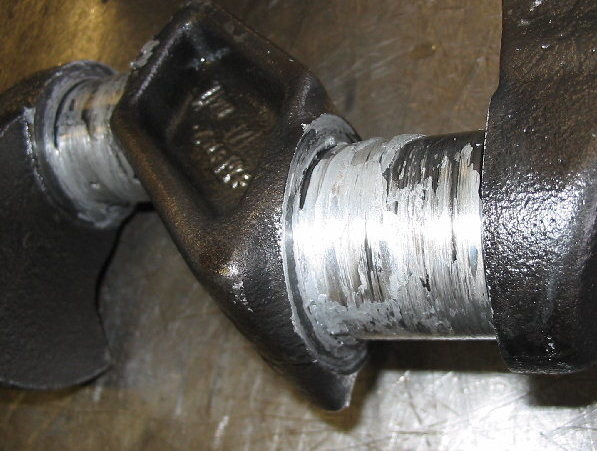
9. Тестирование хладагента на кислотность и влажность. При необходимости замена масла. Смесь воды и масла, особенно новых синтетических масел, приводит не просто к отклонению показателя рН, но и снижает трибологические свойства масла. Снижение этих основных качественных показателей приводит к снижению качества работы смазываемых поверхностей, что значительно снижает ресурс оборудования;
10. Проверка и регулировка подогрева аппаратов. Независимо от исполнения установки, подогрев различных аппаратов требуется для нормального запуска и работы;
11. Проверка работы датчиков уровня жидкости и масла. Защитные функции этих датчиков должны быть постоянно исправны;
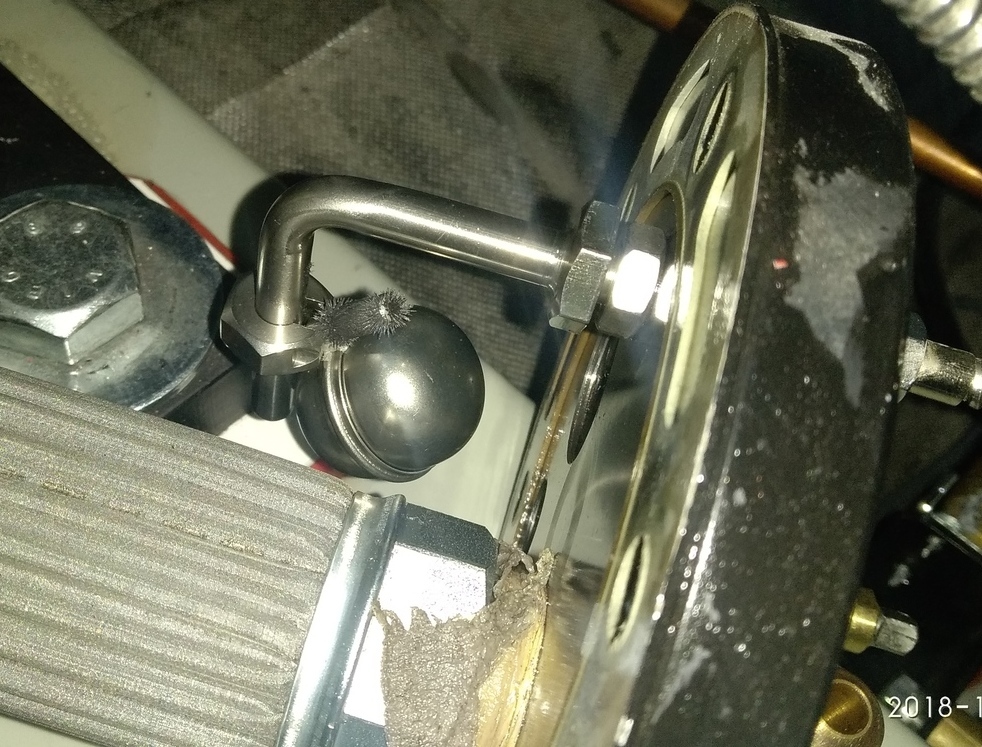
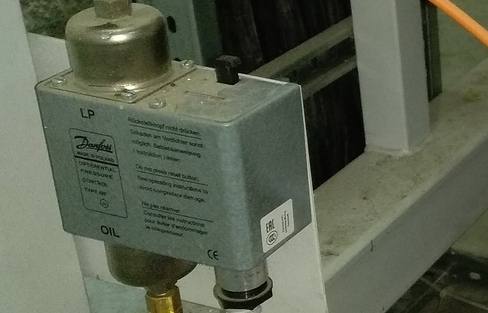
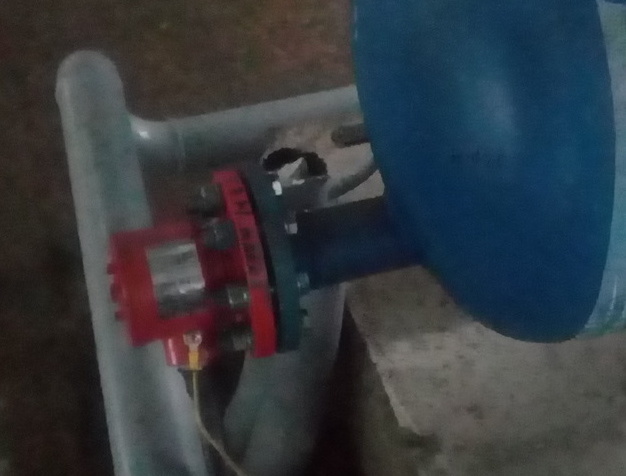
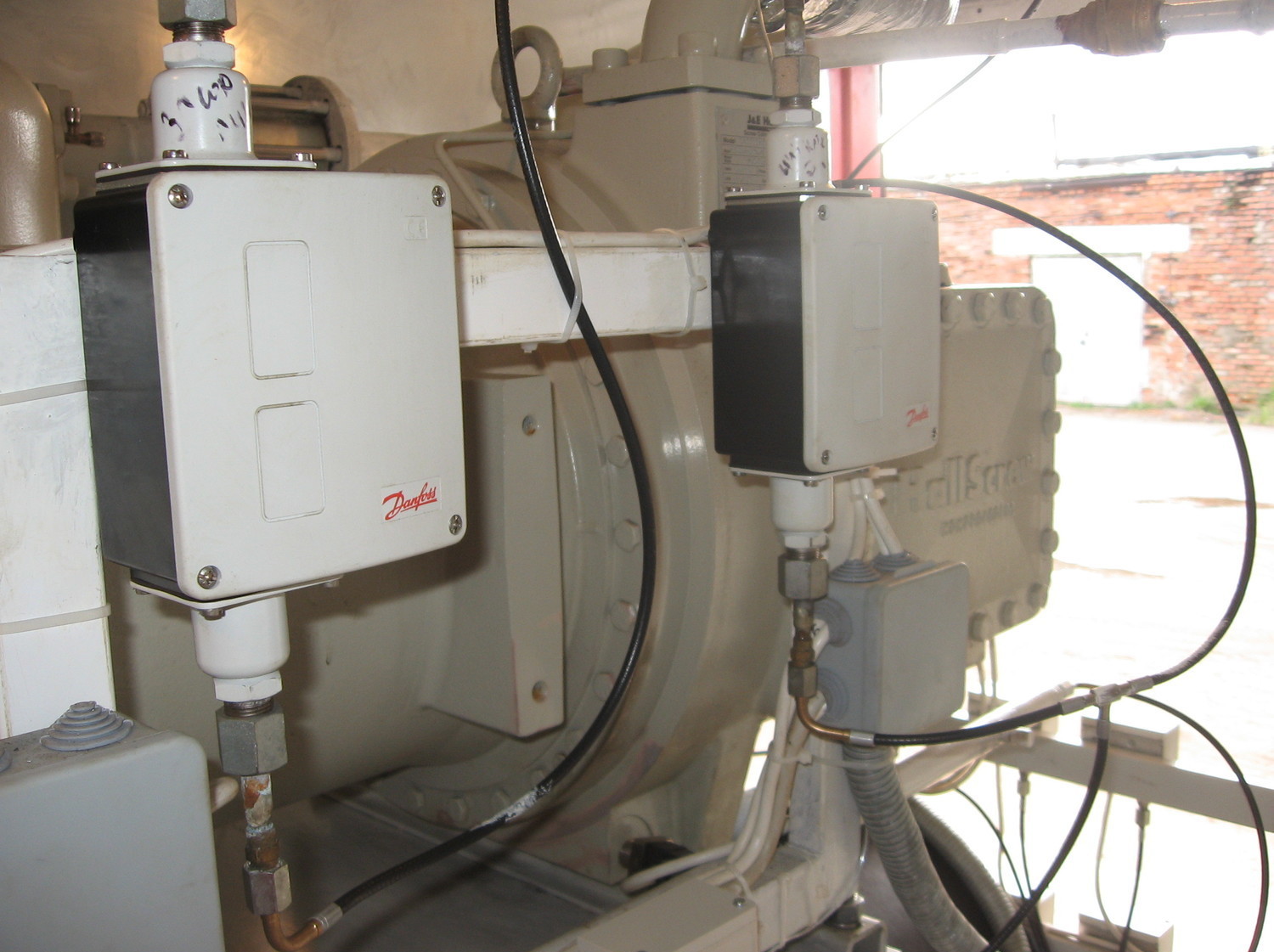
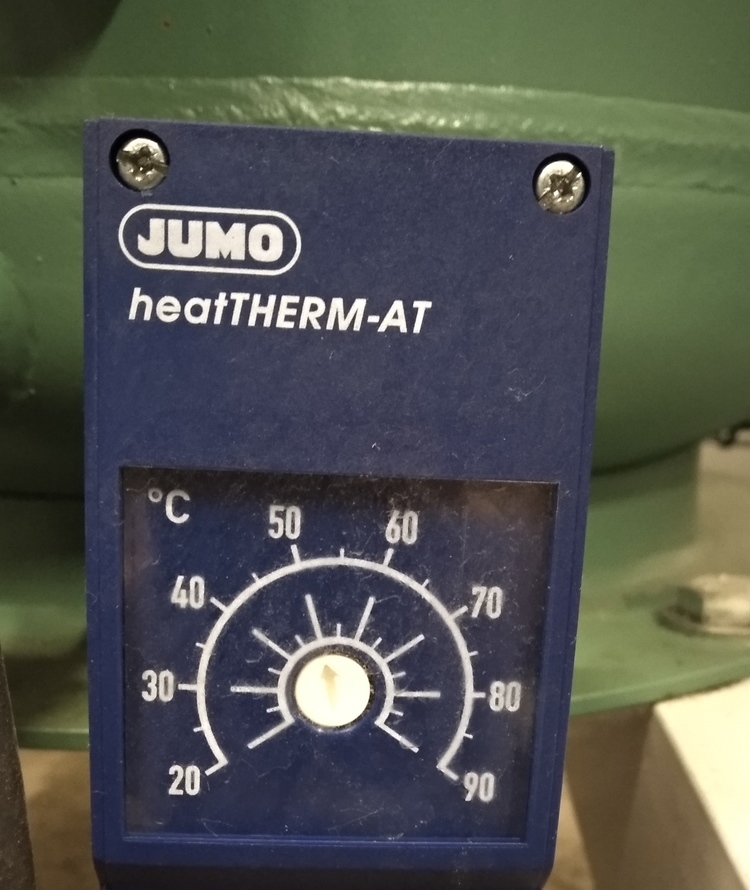
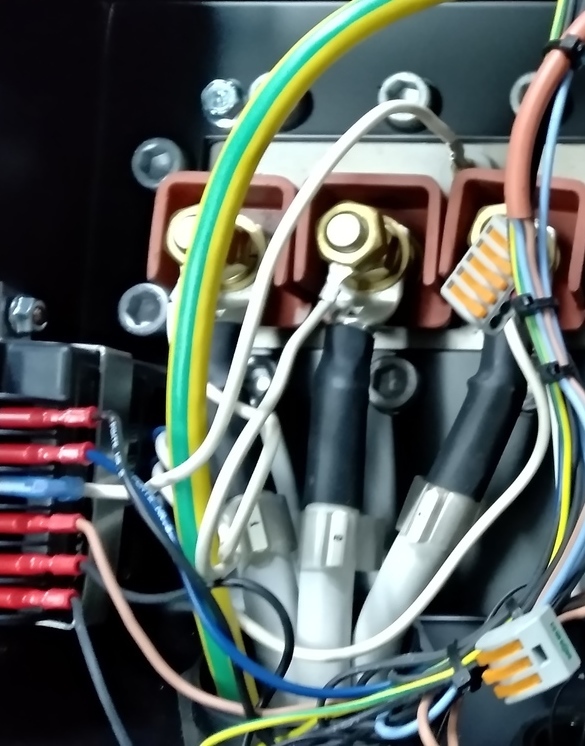
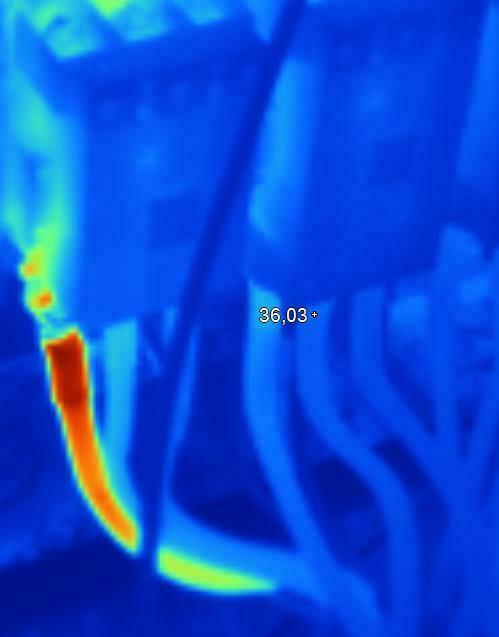
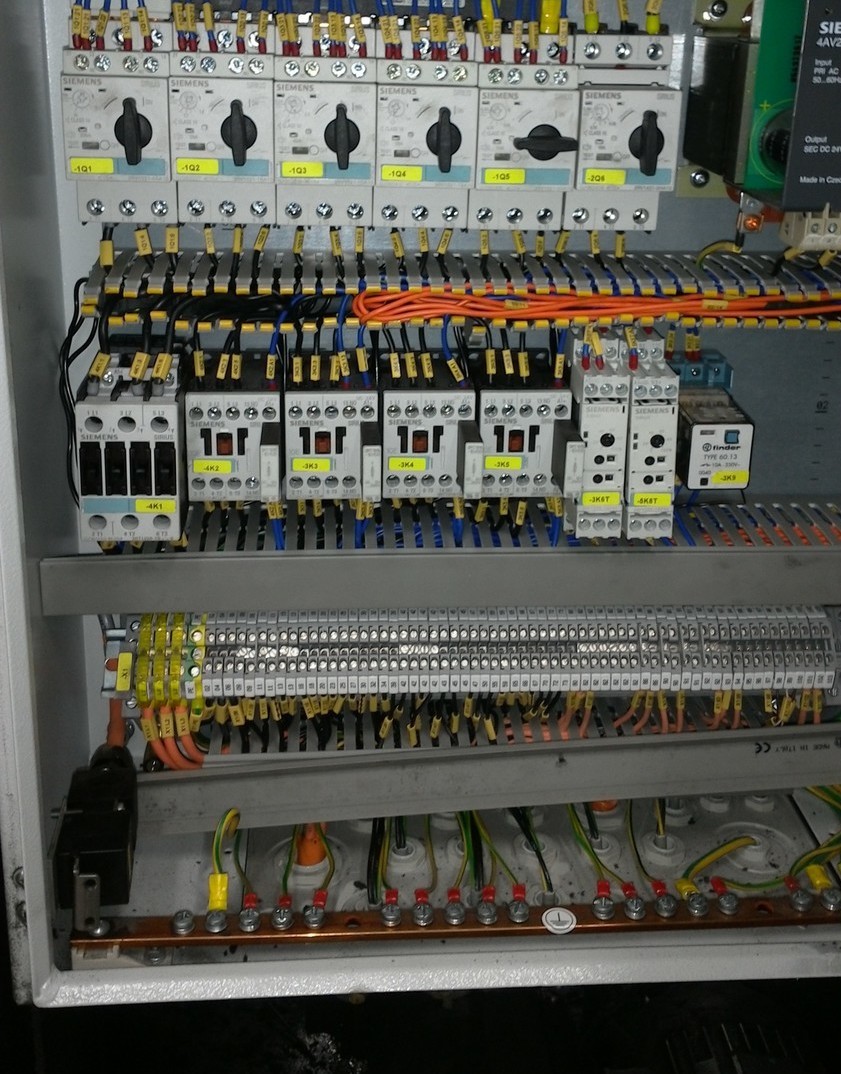
12. Проверка работы реле высокого и низкого давления. Это устройства защиты не только самого оборудования, но и персонала работающего с ним;
13. Проверка теплообменников на загрязнение и коррозию. Очистка при необходимости. Возможны варианты чистки поверхности как с разборкой теплообменника, так и без неё. CIP-мойка.
14. Проверка работы тепловых защит компрессора (тепловое реле/терморезисторы);
15. Общая проверка системы защиты компрессора. Как правило, система защиты компрессора не ограничена только защитой по давлению и температуре;
16. Оценка качества работы холодильной машины. По показателям потребляемой мощности в сумме с оценкой мощности;
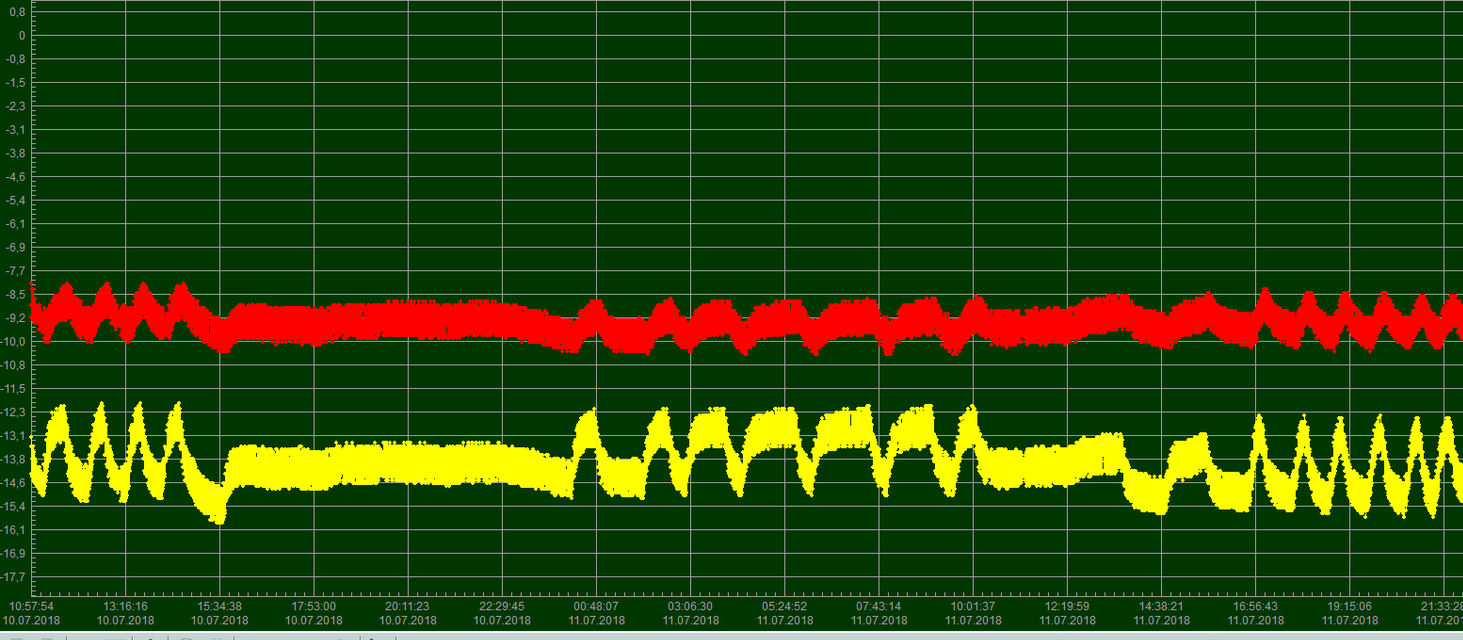
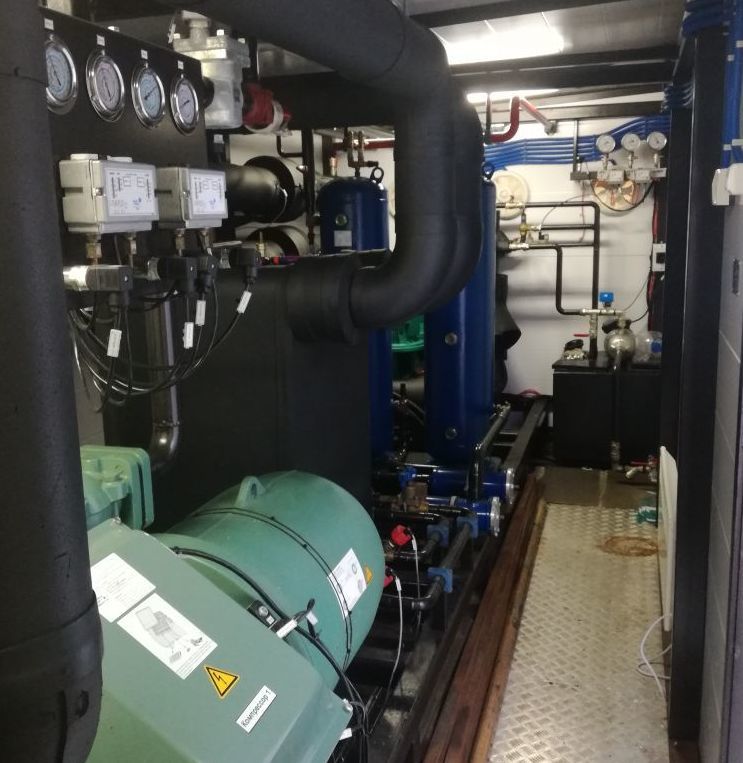
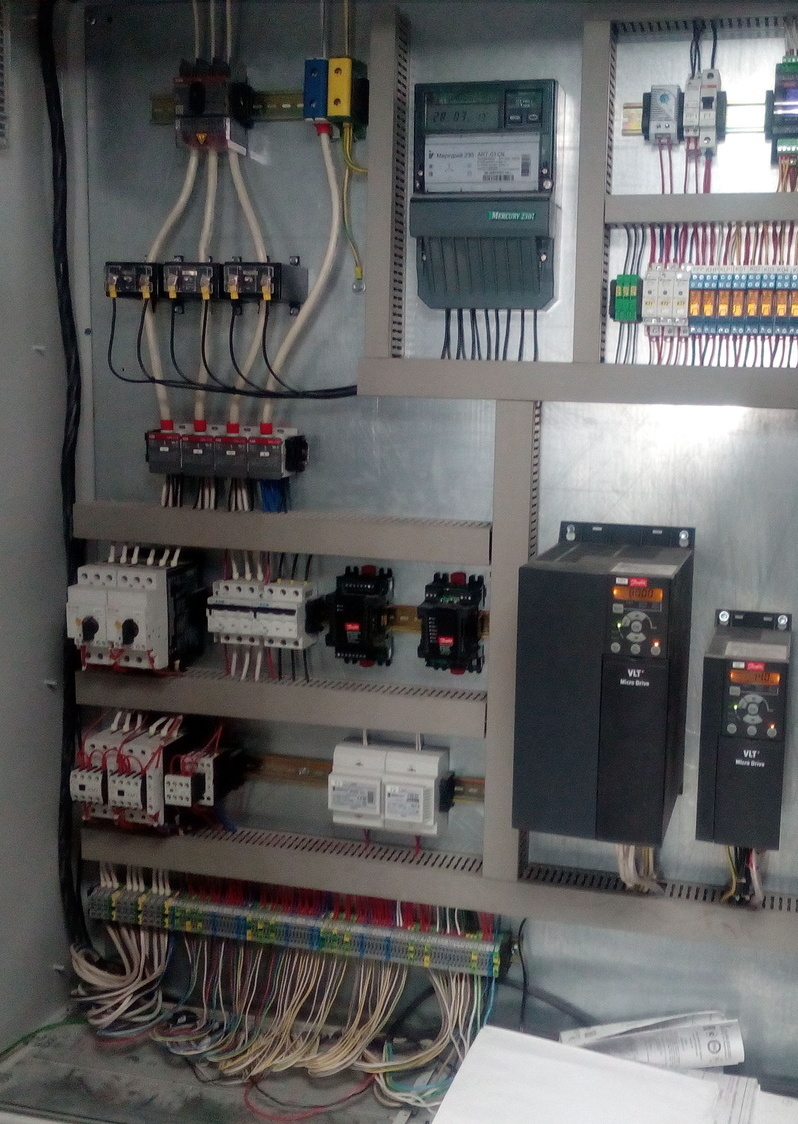
Управление и регулировка
1. Проверка проводов и кабелей на отсутствие повреждений. Сопротивление изоляции;
2. Проверка и протяжка клеммных соединений в щите управления агрегатом. Тепловизионная съёмка;
3. Проверка пусковой аппаратуры компрессора (УПП, софтстартер, «звезда-треугольник»);
4. Проверка реле и пускозащитной аппаратуры основных узлов агрегата;
5. Проверка автоматических выключателей и магнитных пускателей;
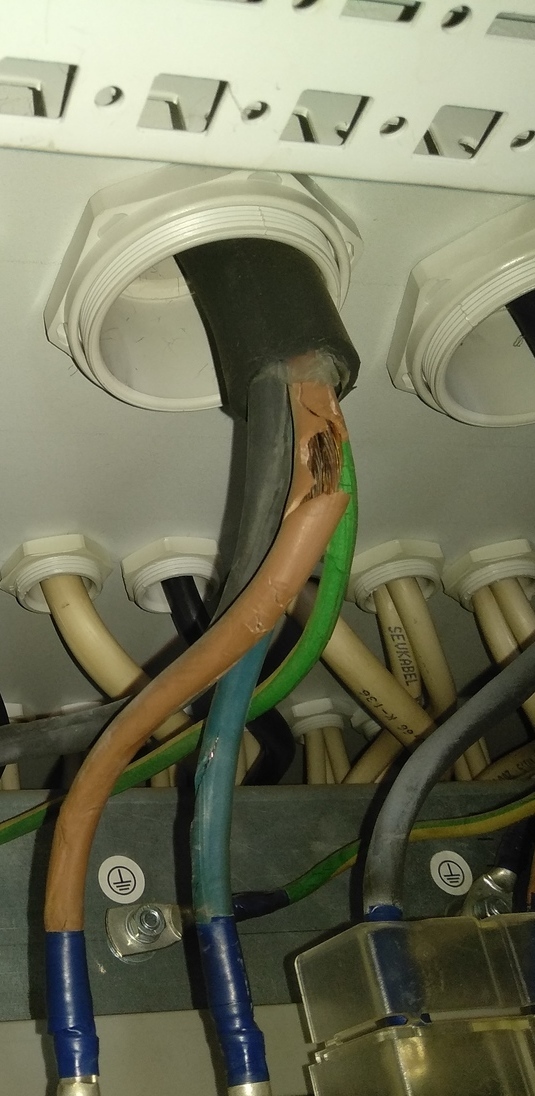
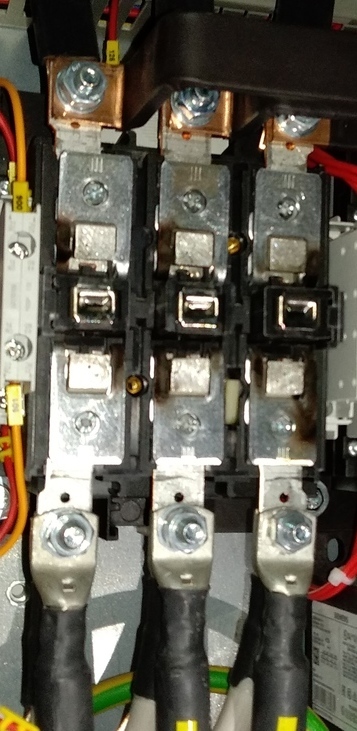
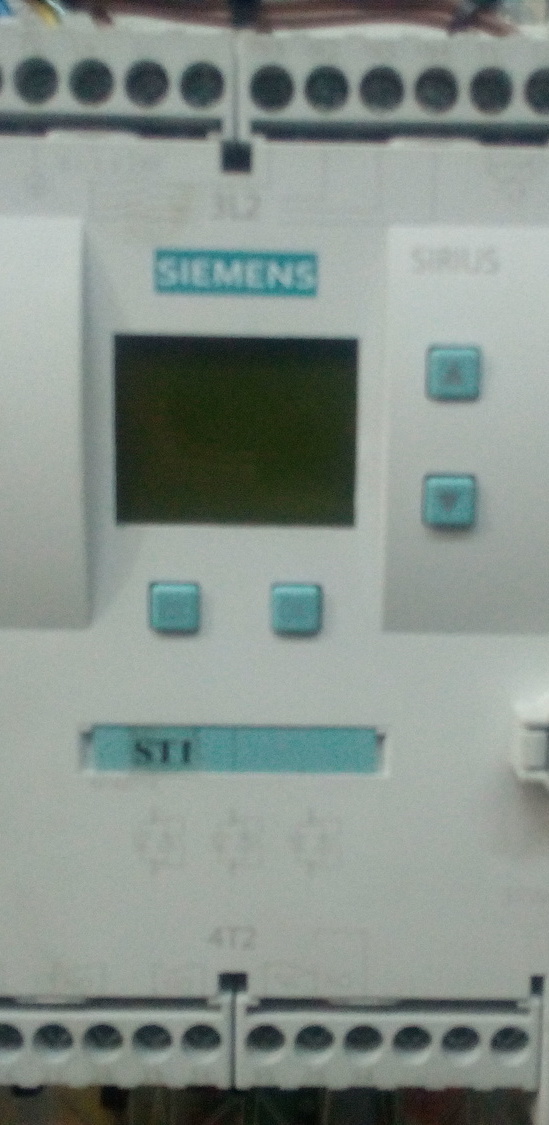
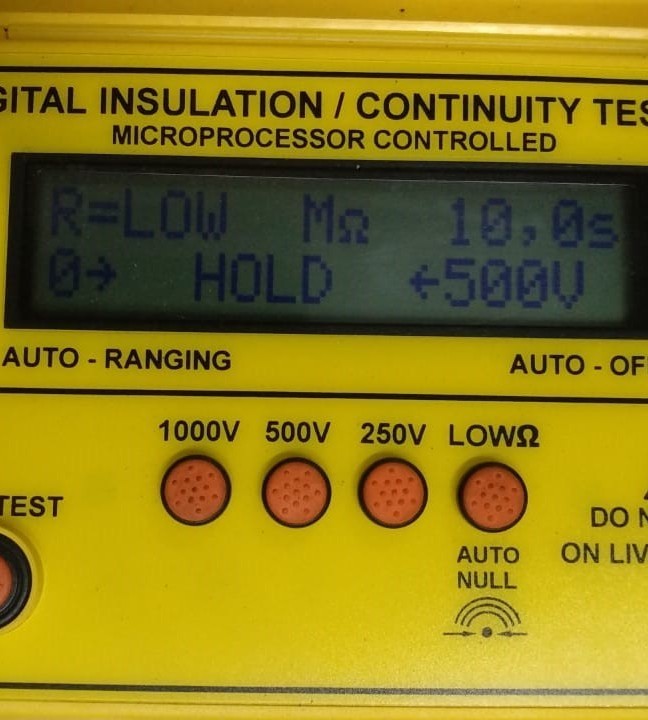
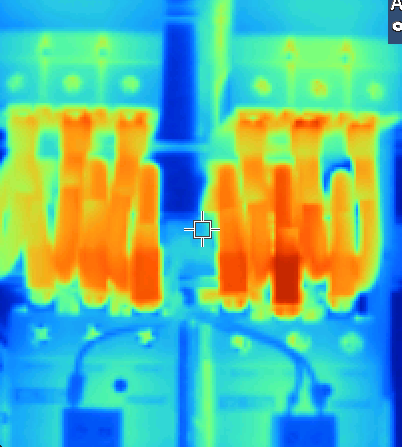
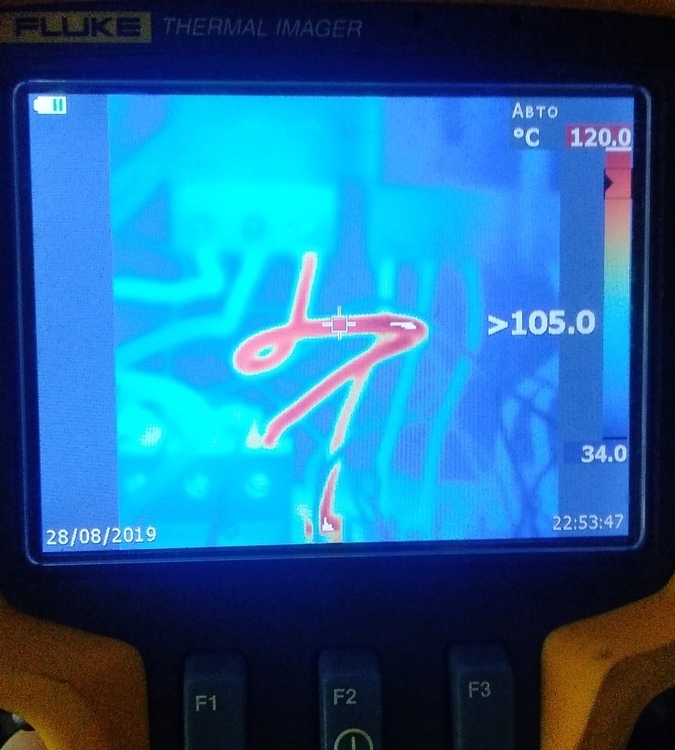
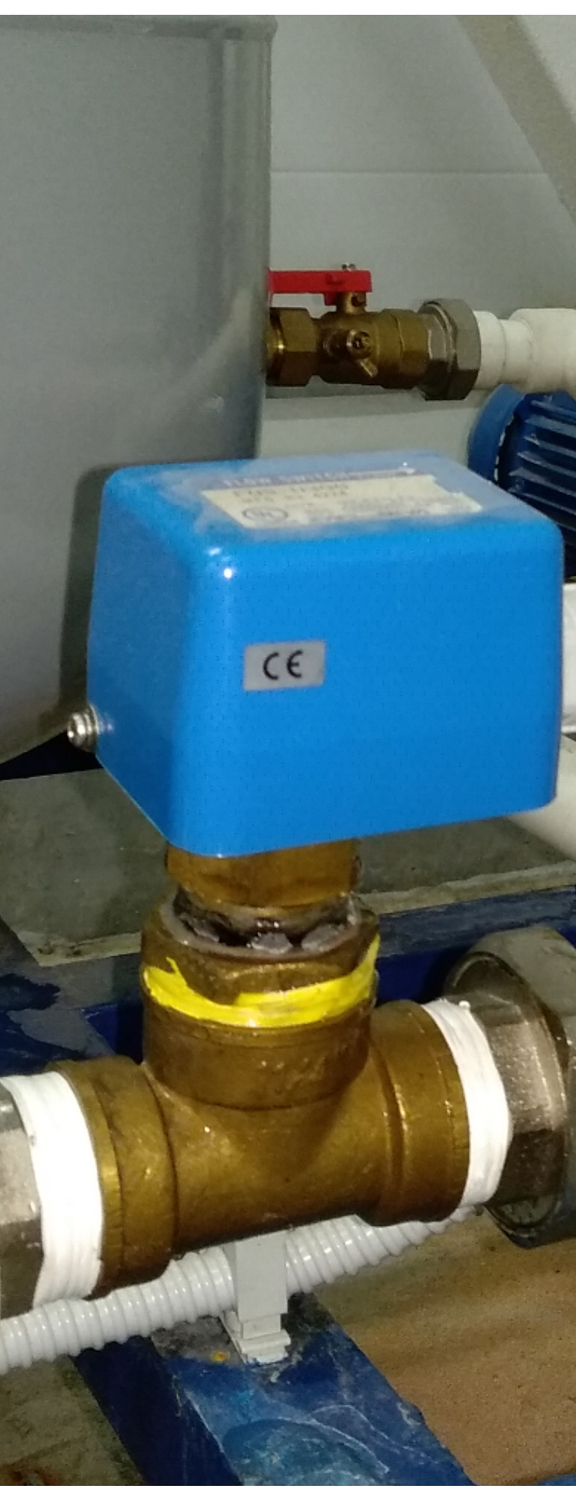
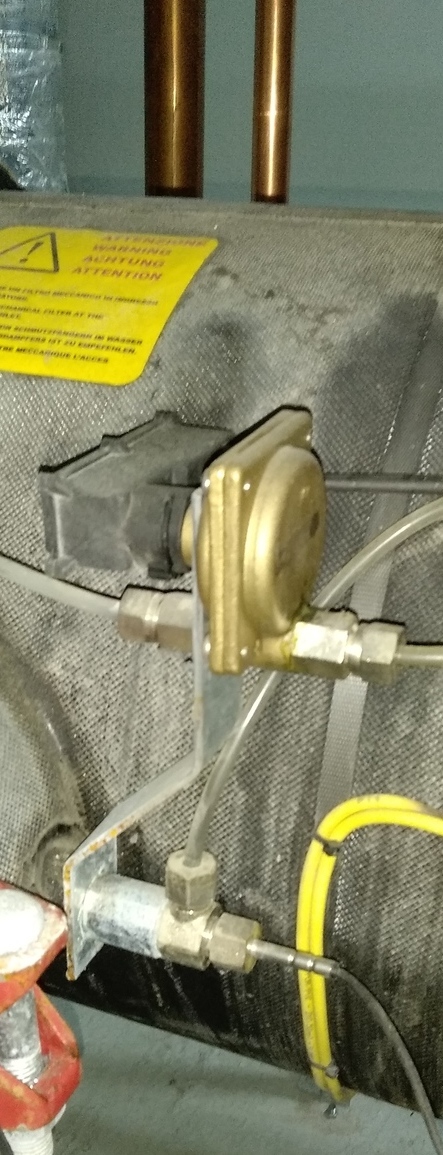

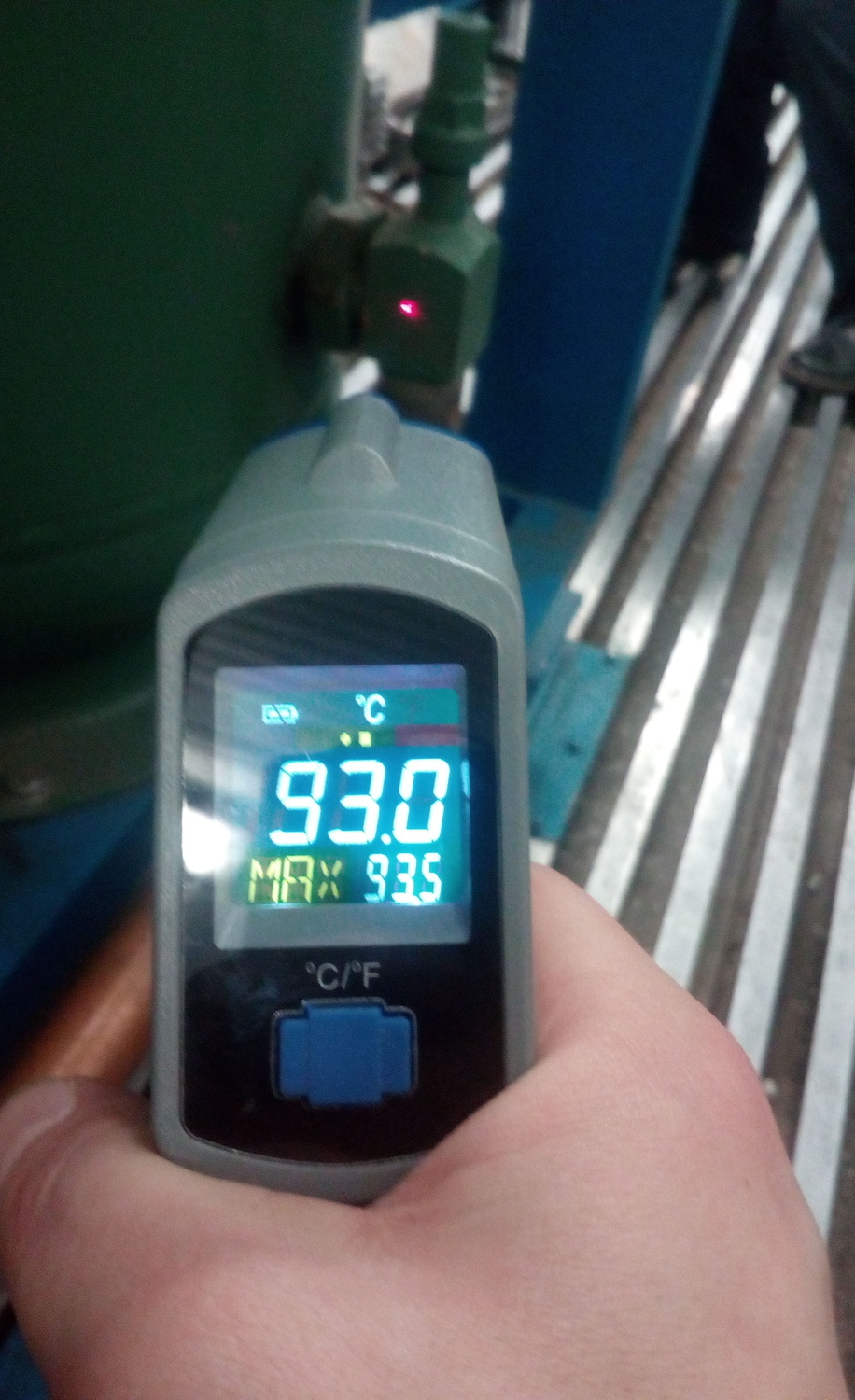
6. Проверка работы устройств защиты по потере потока тепло-/хладоносителей. Реле протока, дифференциальные манометры;
7. Проверка функционирования внешней аварийной сигнализации;
8. Проверка значений температур в контролируемых местах;
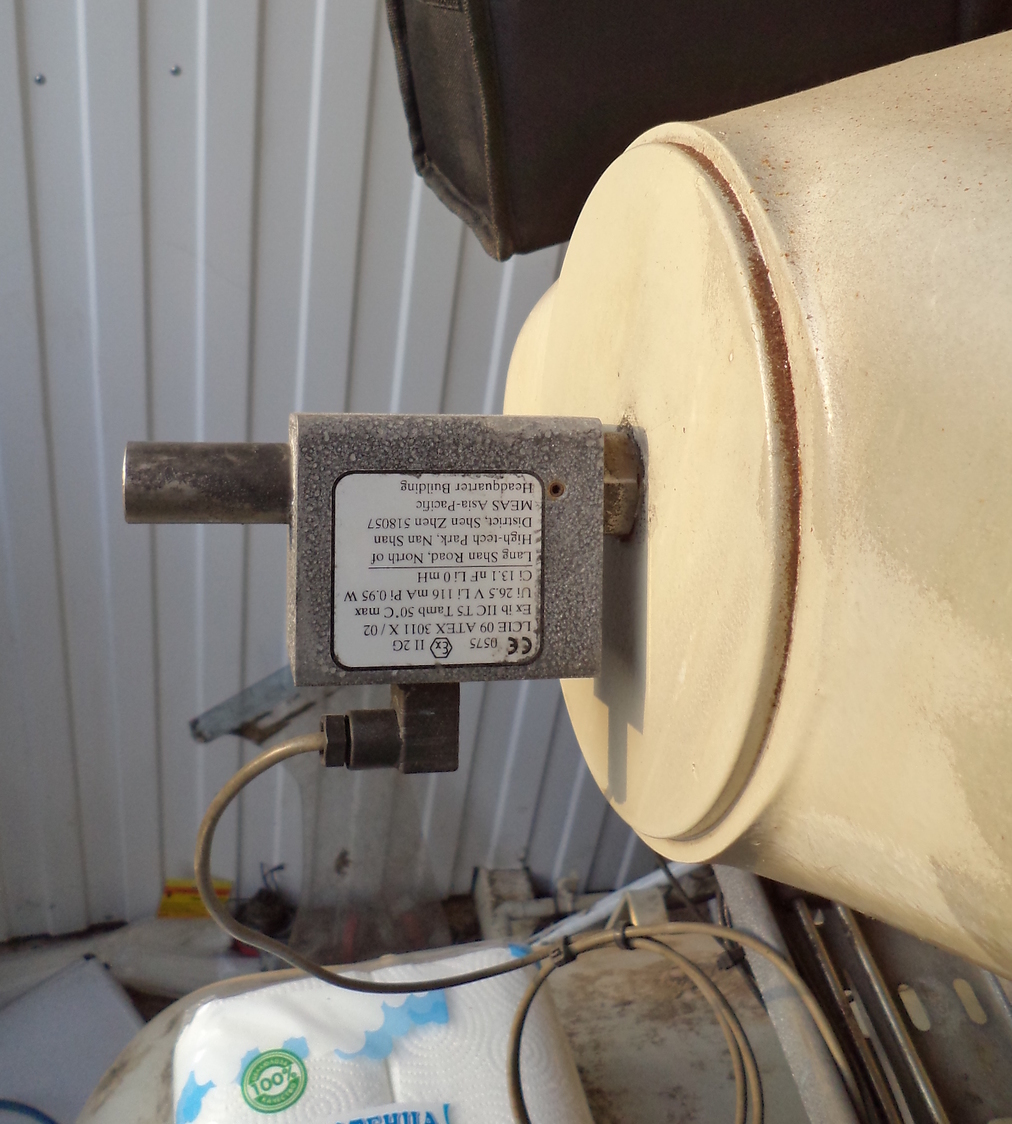

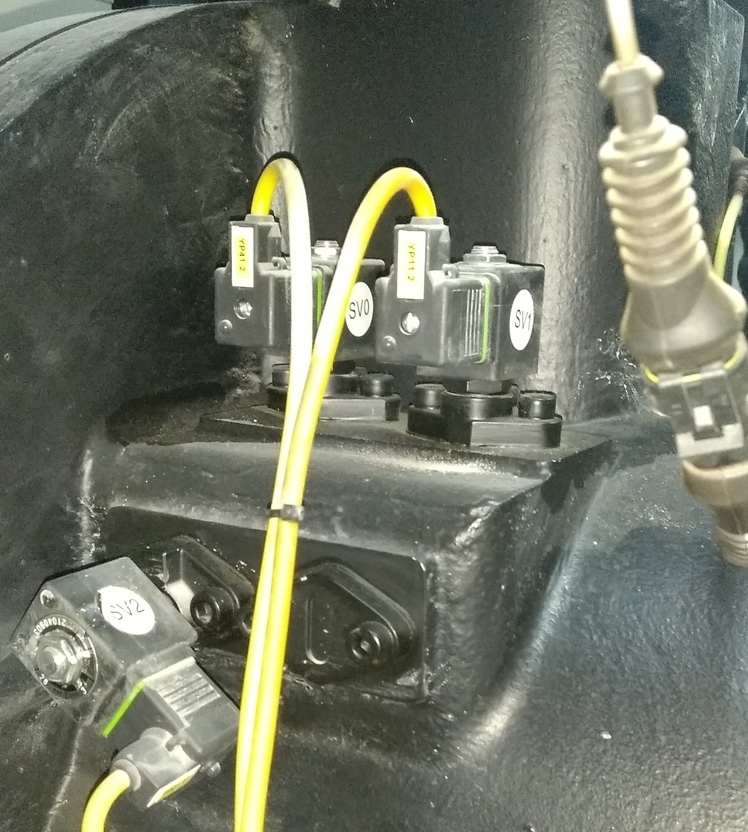
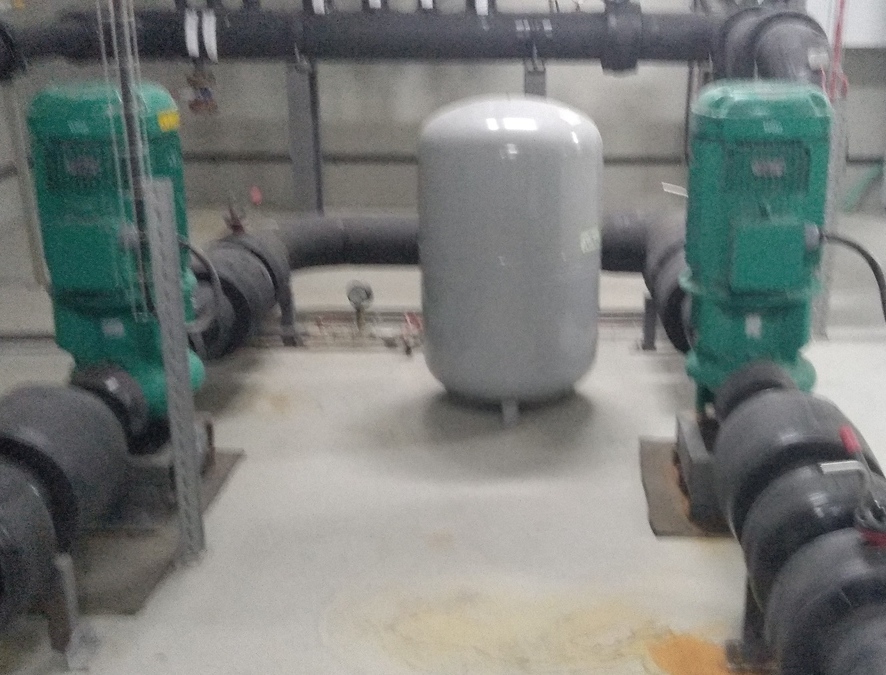
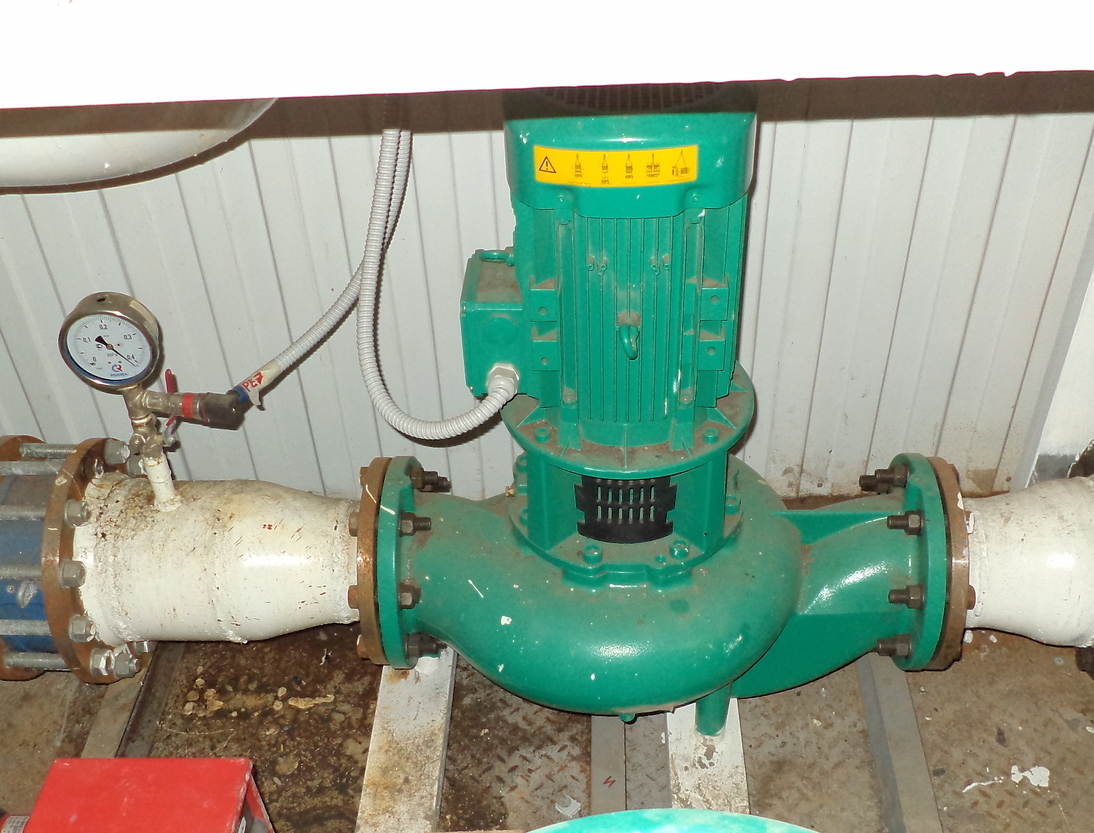
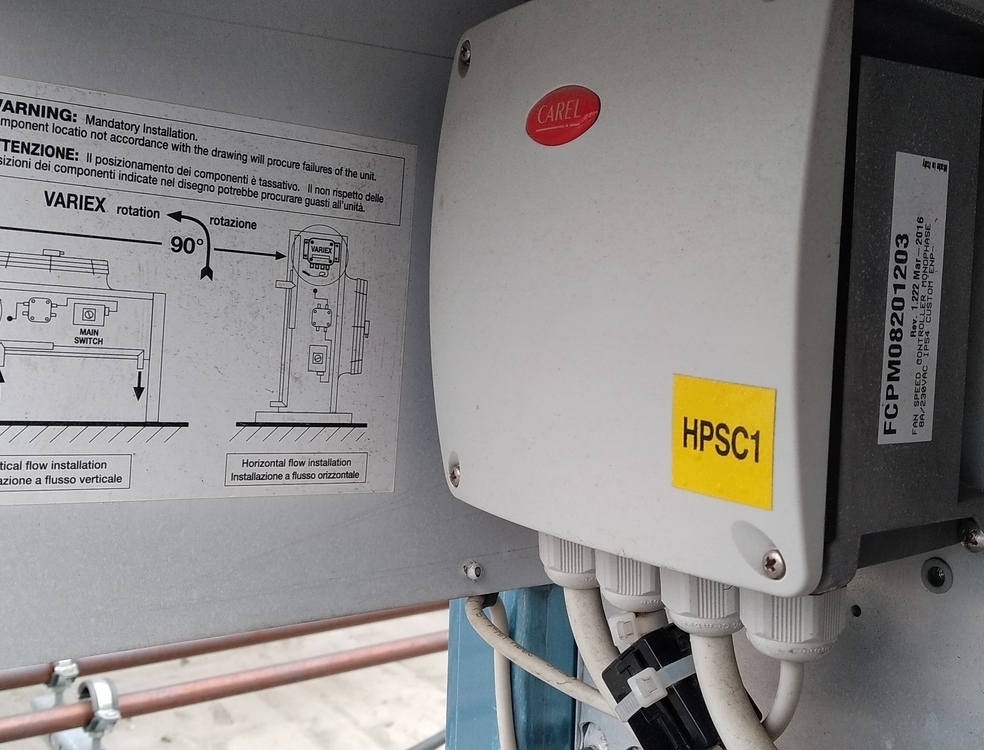
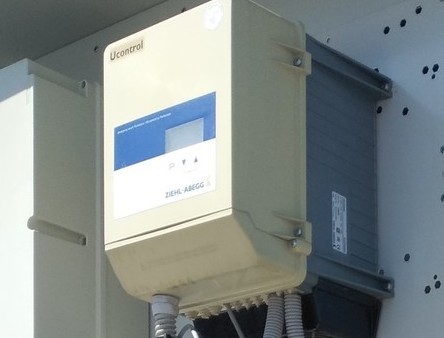
13. Проверка рабочих токов электропотребляющих узлов водоохлаждающей машины;
14. Контроль несимметрии напряжений и токов, проверка параметров питающей сети и блокировок;
15. Проверка срабатывания защит и блокировок вспомогательных устройств;
16. Тестирование промышленного охладителя жидкости (если есть необходимость/ по запросу);
17. Проверка плотности (температуры замерзания) тепло-/хладоносителя;
17. Проверка и настройка системы диспетчеризации (если она установлена).
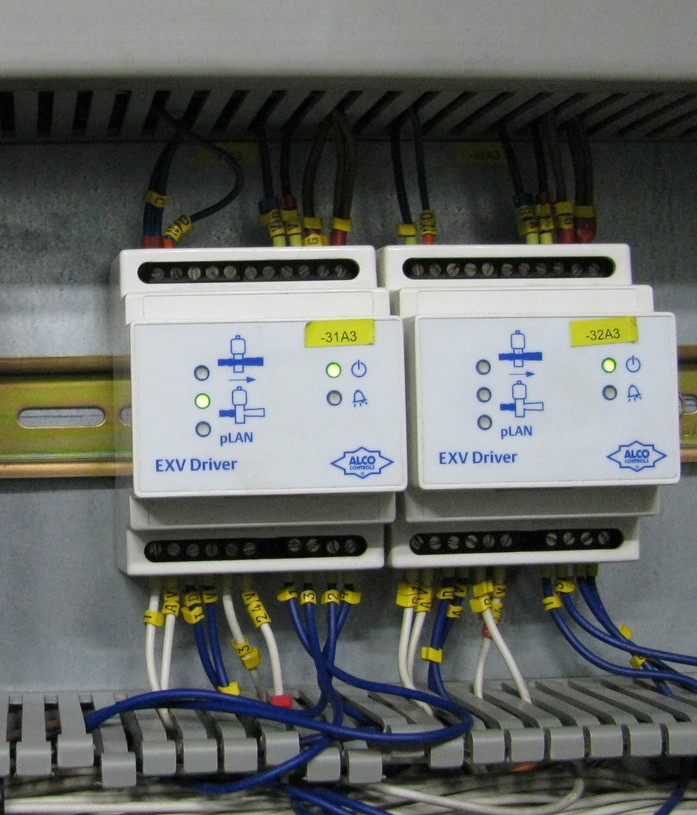

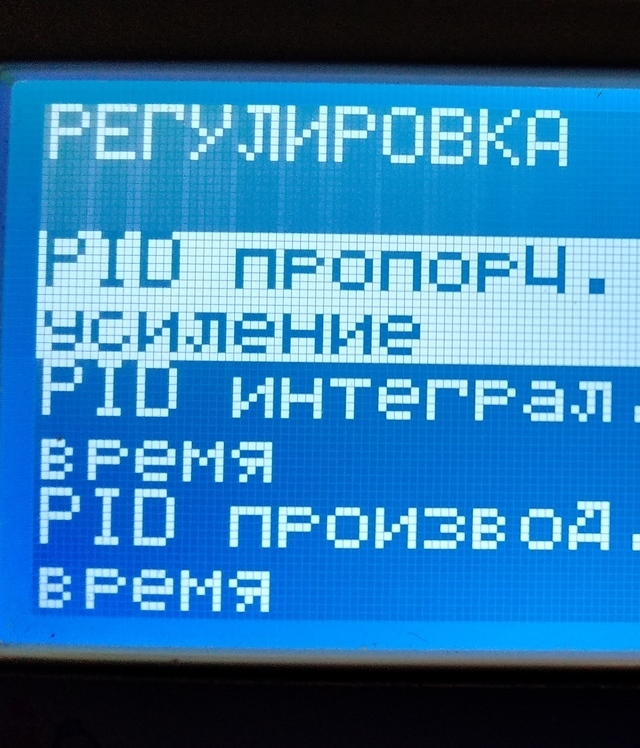
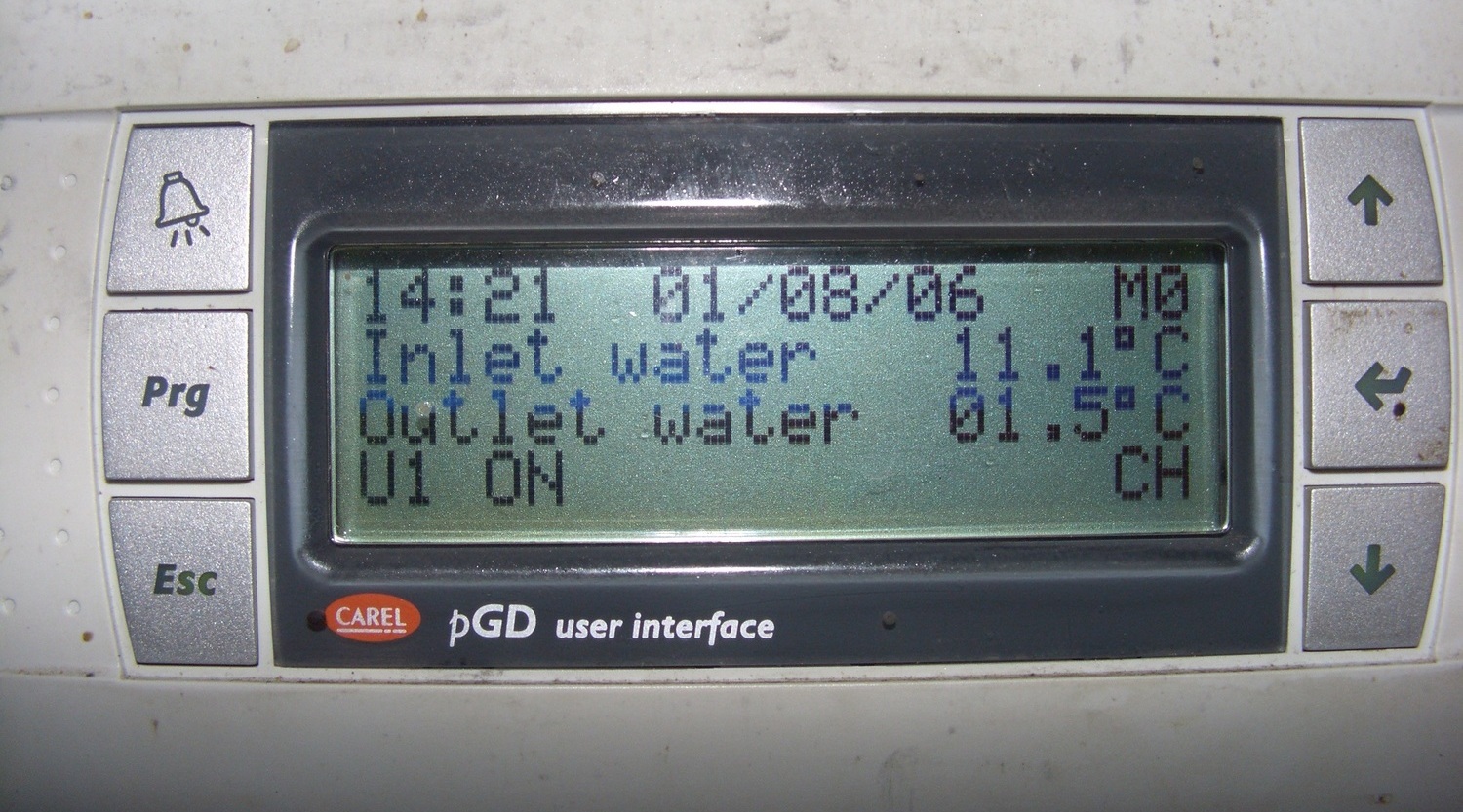
Охлаждение жидкости от пары кВт до нескольких МВт
Обслуживание холодильного оборудования
Обслуживание холодильного оборудования
Типовые системы охлаждения жидкости с затопленными испарителями, на базе поршневого и винтового компрессоров
Схема с открытым поршневым компрессором и двумя пластинчатыми теплообменниками. Рабочее тело дросселируется в поплавковом регуляторе высокого давления, используя уровень в нижней части конденсатора как усилие, открывающее дроссельный клапан. Данная схема, как и схема для винтового компрессора, носит название гравитационная или безнасосная. Процесс дросселирования происходит в самодействующем поплавковом клапане.
Схема с открытым винтовым компрессором и двумя пластинчатыми теплообменниками. В данной конструкции функции охлаждения масла и отвод тепла от конденсирующегося пара совмещены в одном теплообменнике, что упрощает конструкцию установки. Рабочее тело дросселируется в поплавковом клапане высокого давления за счёт уровня в нижней части конденсатора.
нажмите на изображение для увеличения
1
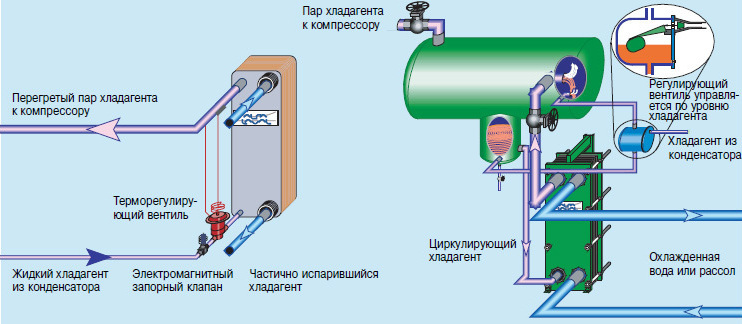